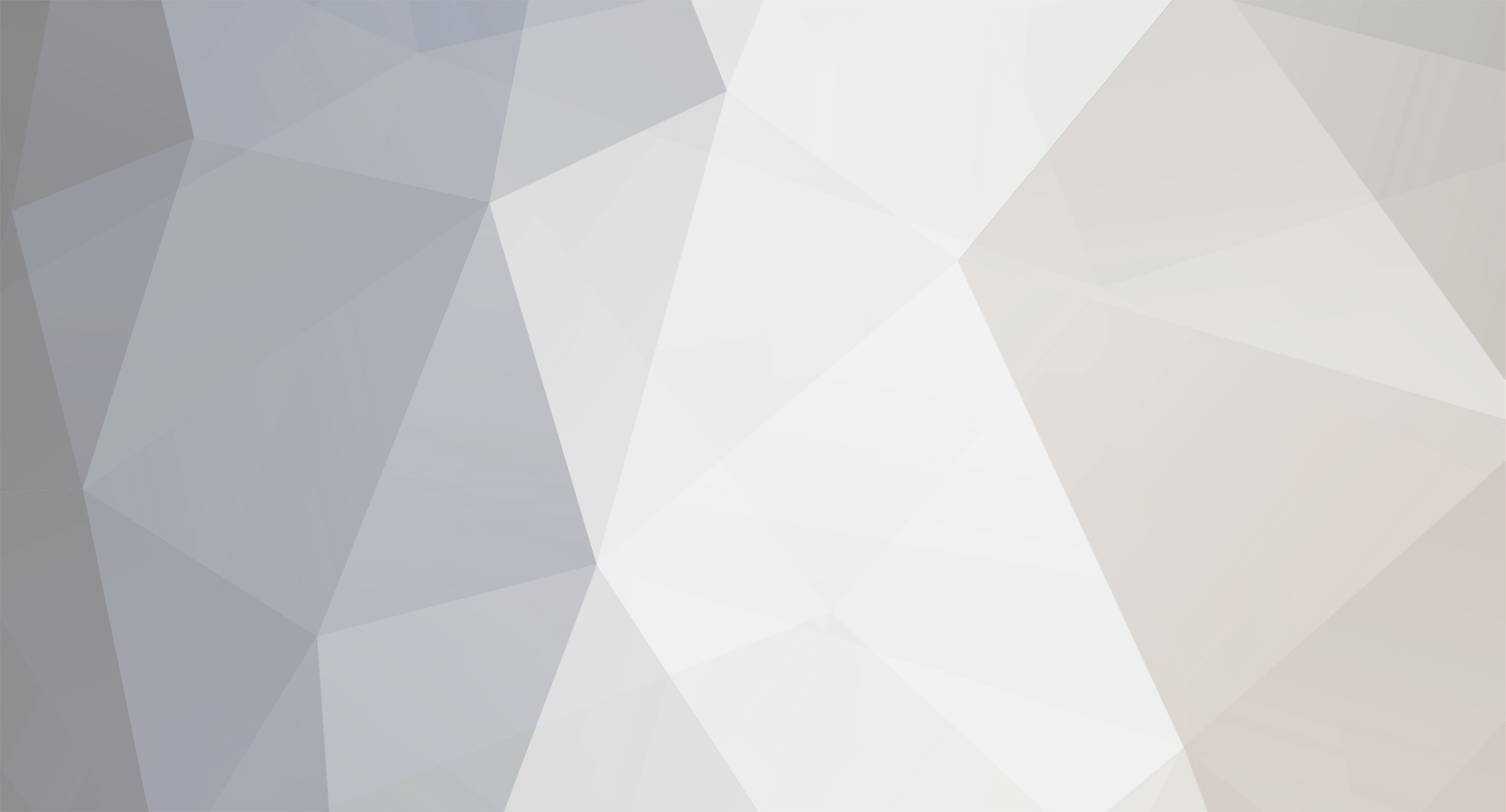
-
entries
0 -
comments
0 -
views
198
About this blog
The excavator hydraulic system runs slowly, which is often called underspeed. Slow is not working, but not up to the system requirements, so the troubleshooting is difficult, and there are many kinds of situations. The following is a summary of the hydraulic system underspeed of the two cases and specific reasons for your reference.
01. The adverse effect of hydraulic pump underspend
The underspeed of hydraulic pump actuator includes two situations:
◉ The rapid movement when the speed is not fast enough, cannot reach the design value and the new hydraulic pump regulation value.
◉ Under a load of its working speed with the increase of load significantly reduced, especially large hydraulic pumps and hydraulic pumps with a large load, this phenomenon is particularly significant, the speed is generally related to the size of the flow.
The underspeed first affects the production efficiency and increases the circulating working time of the hydraulic pump. Underspeed phenomenon in the large load often appears to stop the movement of the situation will affect the normal operation of the hydraulic pump. For hydraulic pumps that require rapid movement, such as surface grinders, insufficient speed will affect the roughness of the grinding surface.
02. Failure cause of underspeed
◉ Fast motion is not enough
This is a common fault in hydraulic pump maintenance, which can be caused by the following aspects.
a. Hydraulic pump output flow is not enough and output pressure can not reach.
b. Overflow valve due to permanent deformation of the spring or the wrong loading into a weak spring, the main valve core damping hole is partially blocked, the main valve core stuck in the small opening position, resulting in hydraulic pump output pressure oil part overflow back to the tank, through the system to the implementation of effective flow is greatly reduced, so that the speed of rapid movement is not enough.
c. Internal and external leakage of the system is serious: the working pressure is generally low when fast forward, but it is much higher than the return oil pressure. When the piston seal of the hydraulic cylinder is broken, the leakage in the two chambers of the hydraulic cylinder is large because of channelization (there is a pressure difference), so that the rapid movement speed of the hydraulic cylinder is not enough, other parts of the internal and external leakage.
d. When fast forward, the resistance is large, such as guide rail lubrication oil, guide rail insert pressing plate is adjusted too tight, hydraulic cylinder installation accuracy and assembly accuracy is poor, resulting in increased friction resistance.
◉ Reasons for the obvious decrease in the working speed
When working feed, the working speed is obviously reduced under the load, even if the speed control valve (throttle valve, etc.) is still so, from the following aspects of analysis and maintenance.
a. Under the load of the system, the working pressure increases, the leakage increases, and the adjusted speed decrease due to the increase of internal and external leakage.
b. System oil temperature increases, oil viscosity decreases, leakage increases, effective flow decreases.
c. The hydraulic system design is not reasonable, when the load changes, the flow into the hydraulic equipment implementation components also changes, resulting in a change in speed.
d. Oil mixed with impurities, blocking the flow control valve orifice, resulting in reduced working speed; When blocked and open, resulting in speed instability.
e. There is air coming into the hydraulic system.
03. Elimination of underspeed
◉ Eliminate the hydraulic pump output flow is not enough and output pressure is not high fault.
◉ Eliminate the overflow valve and other pressure valves produced by the pressure can not go up the fault.
◉ Find out the location of internal leakage and external leakage, eliminate internal and external leakage, replace the worn parts to eliminate internal leakage.
◉ Control the oil temperature.
◉ Clean parts such as flow valves and replace oil in time if oil contamination is serious.
◉ Identify the cause of hydraulic system air intake and remove air from the hydraulic system.
04. Maintenance advise for hydraulic system
◉ Keep the normal oil level high. A level gauge should be set in the tank for frequent observation and refueling.
◉ Check the oil performance regularly, and replace and clean the oil tank in time if it fails to meet the specified requirements.
◉ The oil filter should be cleaned frequently to ensure smooth oil suction.
◉ After the oil pump works for a period of time, the installation screw or valve screw of oil inlet and outlet may become loose (due to vibration).
◉ The maximum hydraulic impact force of the system shall not exceed 14Mpa.
◉ In order to maintain the system, it is necessary to know the relationship between the oil temperature in the tank and the ambient temperature. The highest temperature in any part of the system must not exceed 90 degrees.