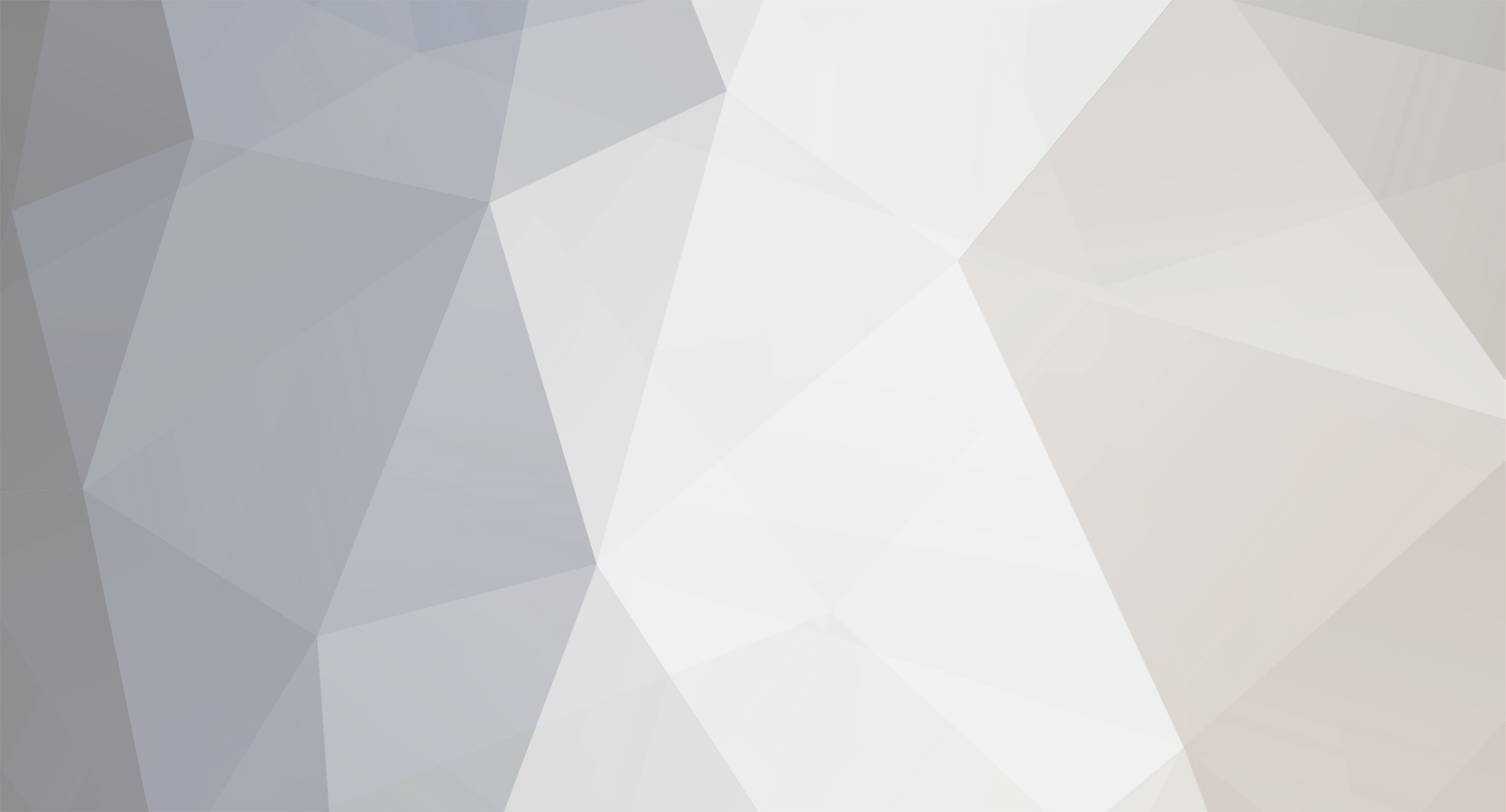
monokinetic
-
Posts
325 -
Joined
-
Last visited
-
Days Won
5
Content Type
Profiles
Forums
Blogs
Gallery
Posts posted by monokinetic
-
-
yes, the MBFM application doesn't output the 1kHz tone, instead you should be able to trigger an epiano sound, which is located in internal EEPROM (so, it should even work w/o BankStick).
OK then something is quite wrong because I cant trigger anything over MIDI. I just get a low buzz, regardless of the app on the PIC.
Hope that you've used "Smart" mode during the application upload - just to ensure that it was really uploaded.Of course smart mode is on when I'm uploading to the core :)
I double checked the core functionality this evening using the interconnection app, each pin is going fine from the core to the OPL3 connectors.
yes quite hot, and the IC3 and IC5 TL074s. The other TL074 seems fine. I tried swapping all TL074s around to be sure it's not chip related. I will still buy some more tomorrow to be double sure....
yes, it is
OK, just checking. Some more silly questions:
I don't have things in a metal box at the moment, just on my work bench. I've not done much with things that make sound with AC based PSU's before. Would that make a difference?
Plus, something that seems weird to me is that Duggles schematic and the original say that the non-live pin, where the AC comes in to the part which makes the DC power, is also where audio ground connects. That is correct isn't it?
Best
Dave mK
-
Hi Thorsten,
As always thanks for taking the time to reply, I really appreciate it.
I have spent some time over the weekend to try and narrow down what is causing this. I followed your suggestion of removing IC3 and testing audio outs 3 and 4. When I switch on there is no sound for approx 5 seconds, then there is a faint sound. I generated a 1khz test tone in software to compare with what I hear, it is pretty close but very very quiet. I tried to upload the MBFM1.1a app. after this, but it seems to output the same sound. I would guess that if everything was OK I would be able to upload the app and send MIDI to trigger some other sound? (by the way I have no bankstick attached at the moment, does the FM boot up with some initial sound or not?)
Some other findings:
one of the capacitors close to IC3 had got twisted and the legs were touching. I replaced it but no change.
IC3 and IC5 both get rather hot after 2 minutes of running. Even with only one or the other plugged in, still they get very hot.
Approx 1 time in 5, I switch on and when I measure the +12v line there is -0.74. I reset the power a few times and it comes back to +12v!
I have tried another crystal oscillator this evening, no change.
Oh yes and 1 question to clarify: When I measure the voltage on IC3 or IC5 pins O3 and O4 I have the negative sensor of my multimeter connected to the common ground point (as marked on Duggle's PSU schematic). That's correct isn't it?
Tomorrow I'm planning on buying some other TL074's to eliminate them from the equation. Any other suggestions?
Best
Dave mK
-
Hello all,
well after a few evenings of staring at the OPL3 circuit board I'm a bit stuck.
Current setup is a CORE v2, OPL3 and duggle's AC wallwart to +/- 12v +5v PSU.
Testing the OPL3 according to ucapps.de I ran without the TL074 first of all. +/-12V all seemed fine. PSU ran for 30 minutes without melting the house down so I unplugged and installed the TL074s. With all 3 plugged in the +12v line dropped to +0.74v. Worrying, so I pulled the power. Through a process of trial and error I have come to the conclusion that this only happen with IC3 plugged in, if I leave it out the board runs without problems. So I have traced every line from IC3, the positive and negative lines plus everything going to the YAC chip. All connectivity seems fine, no obvious shorts. I decided to risk running without IC3 and plugging in audio outs 3 and 4 (which run from the other YAC and TL074 combination) and I either get nothing from the audio outs or loads of static. Yes I'm 100 percent sure that MIOS is uploaded and the FMtesttone app as well.
After reading this thread:
I noticed that TK suggested reading the voltage at the following pins, I have listed my results:
IC3, O4 = -0.84v
IC3, O3 = -0.82v
IC5, O4 = +2.52
IC5, O3 = +2.52
Now the million euro question, any ideas what is going on here!?
TIA
Dave mK
-
I had a feeling that would be the case, just wanted to be sure before frying anything :)
so I will connect up the cables this evening with a bit more confidence, thanks.
D
-
Hi all,
I am following Duggle's power supply, as seen here, using a 12 V AC powerpack / wallwart. The problem is that the wallwart was supplied with bare cables and no markings what could be ground, so I can't work out what to connect to the ground of my breadboard of Duggle's circuit!
I haven't done any AC stuff before so bear with me here: with a DC PSU I would measure across + and - and look at the polarity shown on my multimeter. I have an AC setting on the multimeter and I have used this to measure across both outputs on the wallwart, but connected either way the multimeter shows no polarity. Any suggestions?
I presume it does matter which is negative and positive with such a wallwart?
Thanks in advance for any help
Dave mK
-
Hi,
You probably know about this already, but just in case you don't:
http://www.musicfromouterspace.com/analogsynth/SOUNDLABMINISYNTH/soundlab.html
Must admit that I haven't built a whole one but I did adapt some of the building blocks on to stripboard and they worked well for what they are. Not sure if it will replace a classic Roland but it's one of the most built DIY analogue synths that I've seen (BTW I can't remember if it uses obscure tempco's, not much time to research I'm afraid!).
Also Ray sells PCB's for it online, which would speed things up....
HTH
D
ps personally I don't need a synth, so I'm going to build another WSG :)
-
TK:
sorry my reply is delayed, my machine is currentl burried in an exhibition piece (long story, midibox is invloved!)
no hope to get the pic image just now. i should be able to get at it next week, just for your interest i will pm it....
apologies for the delay!
d
-
TK: Thanks for your vigilence, as ever! I have a feeling I read the PIC into P18 before I flashed, I can PM it if you like?
STRYD: I'm in Prague, the Czech Republic - Mike Germany somewhere. I don't imagine there would be too many security checks.
In fact, they don't check at the Czech borders much :)
[sorry couldn't resist it!]
d
-
Hi, just to add my 2 Euro cents worth:
2 weeks ago I think I ran into exactly the same problem. I bought my new 18F4620 PIC from Mike pre-flashed. But because I've been MIDIboxing (yes its a verb now!!) for a while now I bought a PIC burner PCB, just in case....
With PIC 18F452 my MBSEq 2 was running fine, I regularly reflashed the box with MIDIO128 app, something I compiled myself and the shift register tester etc etc. When I put my preflashed PIC18F4620 from mike in exactly the same box (yes I added the extra resistor on the IIC bus before you ask!) I couldnt manage to get MIOS studio or MIDIOX to upload the software. MIOS studio gave me rpecisely the same error message as mjproc mentioned in their 1st post "unexpected upload request". The box constantly sent out the upload request but never seemed to give the first repsonse so MIOS studio abborted the upload. If I turned off smart feedback from the core the whole upload was sent but it never seemed to be programmed into the chip ie it still just sent out the upload request every 2 seconds.
As I mentioned in this message:
http://www.midibox.org/forum/index.php?topic=8673.msg61123#msg61123
after almost 1 week trying to upload MIOS and the app I decided to build my PIC burner. This worked perfectly first time, I then read in the preflashed PIC versus the correct bootloader hex file and P18 reported over 500 errors in the program and (from memory) 8 errors in the device id. I reflashed the PIC with the bootloader, put it into the same hardware, and voila, MIOS studio uploaded the software first time :D
I then used the change ID app to set my device ID to work with the IIC Midi out put, it worked fine. The only problem I have at the moment seems to be connected to the IIC midi, I will save details of this for another post once I have investigated further (need to build my COREV3 PCB and do some fault finding!)
My point is that I think we should double check with Mike re: testing one of his pre-burnt PICs because if I hadn't bought the PICBurner PCB, I would have been totally stuck. Especially as in a few places it is recommended for newbies to buy their PIC preflashed......
I hope you dont think I'm hijacking the thread, but I think there are enough similarities here to investigate further.
Best
Dave mK
-
ooooh i can reply to myself and try to get my post number up!
I put the 18 pin PIC connector on the burner and tested the PIC16F88, it passed fine, 0 errors.
So I set off tracing all the connections and it turns out that silly me didnt realise on the interconnection diagram that SC and SD cross when connected to the IIC :-[
quickly resoldered them and low and behold the TX LED lights up and I can upload apps via the IIC!!!! Whahooooooo :)
only thing that seems a little weird is that even though I have reuploaded the IIC Loopback app via the IIC module itself when I send midi notes from MIOS Studio they still arent echoed back. But to be honest I'm off to finally play with this darn sequencer after years of soldering ;D
best
d
-
Ok now that I have my 18F4620 working properly I am having strange behaviour with the IIC Midi output. The board I'm using is from Mike, only stuffed with thep arts for MIDI output. The core is V2, yes I do have the 1K resistor on J4 :)
I have sent the change device id to 0000 0000 0010 0000, it runs on the box and the screen displays the same Device ID number. Then I send the IIC loopback application, also uploads fine. The box reboots and displays this:
S11 S12 S13 S14
- - - -
From the ucapps page describing the IIC module it is difficult to tell if this display is correct. I would imagine that this screen would tell me if the IIC bus has something at ID's 10,11,12,13. Does my screen indicate the core isn't reading anything at these ID's on the IIC bus?
I change over the MIDI cable to the output of the IIC module, send MIDI from MIOS studio and nothing is echoed back to the MIDI In monitor.
Double checked schematic and boards for continuity between core and the input on IIC, all seems fine.
Double checked for continuity between PIC socket pin 10 and the MIDI socket. The power LED comes on.
Now I'm a bit stumped, any suggestions?
Dave mK
ps I'm off to buy another 18pin socket so I can solder it into the PIC burner. My suspicion is that the PIC16 from mike also isn't flashed properly......
-
Hi Wilba,
Thanks for the reminder, to be honest I have given up with the JDM. I've had it for 3 years an never burnt a PIC successfully. I tried a variety of machines, O/S's etc - no joy.
TO ALL:
Luckily even though it says in various places on ucapps or the forum, just get a PIC from Mike with the bootloaders burnt in, my experience has shown that being able to burn my own PIC is essential. Originally I was using broccoli to burn all of my 18F452's, unfortunately it looks like devlopment of this application has stopped and they won't be supporting 18F4620. I tried all of the recommended software with both JDM and Broccoli hardware (P18,WinPIC800, broccoli software, PICpgm etc) but no joy. Built my PICBurner hardware which I bought just incase this sitaution arose, the hardware worked perfectly first time, hurrah!
Before reflashing my 18f4620, which was ordered preloaded with bootloader1.2 from mike, I used P18
to compare the PIC contents with the bootloader file on ucapps. P18 reported 541 program errors, none in Device or config.
So I removed the CP, erased the PIC and reflashed the bootloader, put the PIC into my MBSEQ et voila, booted first time :)
My main point here is this: If you are tinkering with MidiBoxes I would personally recommend having a PICBurner handy. It is a couple of Euros and a nights soldering but then you are protected against weird problems like I encountered here.
Best
Dave mK
-
Hi all,
I've had my MBSeqV2 up and running for a while, I tested today uploading apps via MIOS Studio latest version downloaded today using one of my standard PIC 18F452. No problems uploading a variety of apps so I'm pretty sure hardware is ok, MIDI cables etc tested just incase. Even checked my Java version, seems to not be beta.
All I have done is swap the old 18F452 for the new 18F4620 and when I boot up the box I see the classic black bars on the LCD. However MIOSStudio is constantly receiving the F0 00 00 7E 40 00 01 F7 every 2 seconds. From memory this means that MIOSBootstrap loader is burnt onto the pic, which is what Mike did for me.
So I went through my usual procedure, trying to upload MIOS1.9d via the MISOStudio software. I have tried all of the ways, using feedback, smart mode etc and constantly get the same behaviour. MIOSStudio receives an upload request, it sends the first block of data then the window shows this:
Error: Received unexpected Upload Request
Sending block 00003100-000031FF
Since then I have tried quite a few different things, reading the PIC in my JDM using the WINPIC800 software seems to say that its reading the PIC. When the read is finished the settings window remainswith FFFF FFFF FFFF FFFF. I have tried reburning the bootloader and it won't work. Although I must say I have never had any joy burning a PIC with this JDM :) I usually use broccoli which now isnt compatible with 18F4620 :(
Any ideas what to try next? I've got a MBHPBURNER PCB ready to build if the worst comes to the worst but its a bit weird don't you think? Could it be something connected to the ID or config bits?
TIA For any suggestions
Dave
-
hiya,
I would recommend uploading the MIDI128 app to test DINS, its on the mios download page.
Once you have it uploaded the screen shows you which shift register and which pin is being read.
This process saved me hours of soldering debugging :)
Best
Dave
-
Wilba:
thanks for the speedy response and the spacing advice! great help :)
I will put some of them on my list to Santa.......
D
-
Hi all,
I am trying to find some cute knobs to finish of my MBSeq, I have used the VOTI encoders. I took one to my local electronics shop and they were surprised to see that the encoder has a flat part to the shaft. Personally I don't think its that uncommon....
after a bit of forum trawling and drooling over various options I think I am going to order the knobs mentioned here:
http://www.midibox.org/forum/index.php?topic=6562.msg41366#msg41366
But before I spend the money can anyone confirm that these knobs will fit ok onto the VOTI encoder shaft with a flat edge?
Plus if I remember albs.de has a minimum order, anyone want to do a group buy?
Regards
Dave mK
-
Hi Uriel,
I did a little bit of research on the G2, I'm not sure you need to get so complicated with your Midi Box and make the MBUC. As I understand it, the MBUC is designed as a SYSEX editor. Sysex is the way many synths without front panels are edited, for example the Matrix 1000 someone is also working on in this forum (JackKaos i think).
I played with a Nord Micromodular a few times and I remember being able to assign a simple MIDI Continuous Controller to almost any parameter. You can use just the simple MB64e application to send such messages. This would give you a front panel for the Nord that can be used to control any parameter you setup a Nord patch to respond to. I think you could also setup buttons to change patches with program changes.
But I also read the page you linked: http://www.rattus.net/~packrat/audio/pages/g2-cont/
This looks like an application which communicates with the Nord through sysex because it gives you feedback ie the screen on the hardware tells you information from the Nord. This sounds cool but using the MBUC you would have to customise the application I think to achieve the same thing.
So the question is: do you want to just have a hardware interface that controls your nord sound parameters for live tweaking of sounds OR do you want a more sophisticated front panel that tells you which patch you have in which slot on the nord?
The main reason I am asking is because the screens are different between the MB64e and the MBUC....
dave m
-
Hi Tk,
I have been lurking on the sequencer threads for a while. I think the mixer map suggestion as a solution for live use would be helpful because it is very often that I want to set up my equipment to play from one state (ie the mixer map) before a sequence starts.
My MBSeq is sitting in bits waiting for some free time to be finished. So this idea may be implemented already.....
But in regards to mixer maps with the sequencer, one thing I have been contemplating as a suggestion is performance controllers. When in song mode I would really like to be able to assign the rotary encoders to control parameters within a sequence. As an example one could then assign the 1st 2 encoders to control the note length of Tracks 1 and 6. The next 2 encoders control Transpose on Tracks 8 and 10 etc. I think it would even be useful to be able to set the encoders to transmit CC's to control synths live in addition to playing back the song.
I feel this would help me to create very live sounding arrangements.
Ok back to work, shame.....
Dave M
-
Hi all,
I followed this thread with baited breath..... and then nothing!
I understand all the theory and am PRETTY confident to build it, but before I start I would like to ask:
Has anyone built this design and used it successfully?
If not then I guess I will have to be a guinea pig ;)
d
-
Hi,
In regards to buttons I got mine from my local electronics supplier in the Czech Republic. You haven't mentioned where you are in Europe, as far as I can tell! You may get more accurate advice with this information.....
I have seen these round buttons mentioned in a few other catalogues as "DT 6" switches. I dunno what that means but if you go here:
http://www.ges.cz/english/index-a.htm
and put DT 6 into the search box you wil see how quickly they can be found. Their pages provide the exact dimensions so you can compare with other switches.
I'm pretty sure this company can accept and ship orders within Europe and they don't seem to have a very big minimum. Maybe easier than reichelt, who knows.
If not stick your country and DT6 switch into google and see what comes up :)
Good luck
d mK
-
cool, I was just checking, didn't want my nice shiney LCD's all frazzled ;D
Thanks for alleviating my worries so quickly!
D mK
-
ok I had read this briefly once but your forum message reminded me to double check......
WOW! That sounds rocking, exactly the kind of thing which will have me soldering again for many hours, wahooo :)
thanks for releasing such comprehensive documentation, I'm looking forward to this one!!
dave mK
-
Hello all,
Well I have everything hooked up for my MBSeq but I think I have run into a power issue. I have a setup the same as TK's, so 2 x LCD's plus 32 LEDs. I have MIOS1.8 and the latest MBSeq app. The only "non standard" thing I have is that I replaced the B40C800, which is unavailable in the Czech Republic, with 4x 1n4007 diodes, as recommended on the forum. I supply the box with 7.5v from a 1000mA wallwart.
Anyway, turning on the MBSeq with everything attached all loads up fine, but after 3 or 4 minutes there is a worrying "too hot" smell coming from the 7805 and its too hot to touch! I did a bit of research through the forum and this seems predictable as the 7805 is only designed to deal with 1a loads. I have checked my LCD's manufacturers website and trawled the net for a datasheet which mentions how much current they draw but I haven't come up with anything. To be sure I know I could break the power lines going to the LCD and use my multimeter in series to measure the current drawn, does anyone know an easier way of doing this though?
Lets assume for a moment that my 7805 isnt happy :) I know maybe you are going to suggest clamping a heatsink to it but I'm a bit worried that it is going to blow, do you think that's likely?
The only other strange behaviour I have from my setup is that when I try to adjust the backlight and contrast trimmers they make almost no difference to the brightness of the screens, which seems a little odd.
I have looked through ucapps for an alternative power supply and I know TK uses the switching P.S.U. for his MBseq, however I don't want such a physically large supply if I can help it. What are other MBSeq builders doing for their power requirements?
I know various people are working on the MBPSU in another thread, I have followed it and I must say it looks perfect for the MBFM which is sitting on my workbench next to the sequencer! But it still uses a 7805 so it doesn't get around this 1a limit.
I did a bit of research about this and came accross the LM317, which seems to handle up to 1.5a so I put a post about this here: http://www.midibox.org/forum/index.php?topic=6300.msg39036#msg39036
It seems that maybe I was considered to be hijacking the thread, hence a new thread here!
So what do you think, should I just risk heatsinking the 7805 and not worry about the heat? Or should I take the plunge and try to build a LM317 based PSU for heavy load Midiboxes?
TIA for any help
Dave mK
ps I just found a message suggesting this as an easyway to up the current:
http://repairfaq.ece.drexel.edu/sam/samschem.htm#schslp2
seems a bit over the top though to me!
-
My 2 displays for the sequencer use together 900 mA and that is too much for 7805 on the core module.
I was just about to start a thread on this and what do I find? Great coincidence, thats what I love about this place :)
I did a bit of googling and found this:
http://www.electronics-lab.com/projects/power/010/index.html
Which is a schematic for a variable power supply based around the LM317. They also have a calculator for working out the resistor values:
http://www.electronics-lab.com/articles/LM317/index.html
which I tweaked with a bit and the final value for R2 seems to be 720. I presume this is in Ohms?
So I will play around with laying this out on stripboard but 1st I have a few questiosn for those more experienced -
I have already bought a power supply for my Sequencer which is capable of outputing DC 5V-15V at up to 1000mA. From reading the above links and the national.com datasheet it seems that the input supply should be 1.5v more than the planned output, which is obviously 5v for the core. So if I input 6.5v that should be sufficient shouldn't it? I presume if I input more the Lm317 will convert this extra voltage into heat......
All the information I have found about designing this type of supply say using a heatsink is essential. I plan on following this advice but I havent ever used heatsinks before. Do I need to use heatsink compound between the LM317-TO220 and the heatsink? Or will it be sufficient to just clamp it on?
BTW the stripboard layout found is here:
http://www.pinkfishmedia.net/forum/showpost.php?p=32069&postcount=19
The image has 2 possibilities, the left one seems to be "standard" whilst the right is more for audio applications. I'm going to use the left one because the core only needs a stable supply. What do you think?
I look forwrad to having my MBSeq on for longer than 5 minutes (ie before the 7805 is hot enough to fry and egg with all those lights and LCD's attached!)
Dave M
MB FM weird behaviour
in Testing/Troubleshooting
Posted
A further update and some more questions:
I realised that I had got confused when taking measurements at OP4 and OP3, I was measuring on the wrong pins, sorry for the wrong info. Currently I measure:
With IC3 and IC5 inserted:
OP3 and OP4
IC3= -10.77 -1.04
IC5= -5.23 +5.72
Which I would guess is quite wrong!
Without IC3 and IC5:
OP3 and OP4
IC3= -0.02 -0.0
IC5= -0.17 -0.33
I haven't had time to get some new TL074s yet. I'm guessing that IC5 has some problems because of the negative voltages on the pins even when there is no chip plugged in. Any ideas?
My current questions:
is there anyway to test if the crystal is working correctly?
is it ok to measure voltages on the YMF262 and the YAC512 chip pins?
what are the expected voltages at the OP3 and OP4 pins?
TIA for any suggestions...
Dave mK