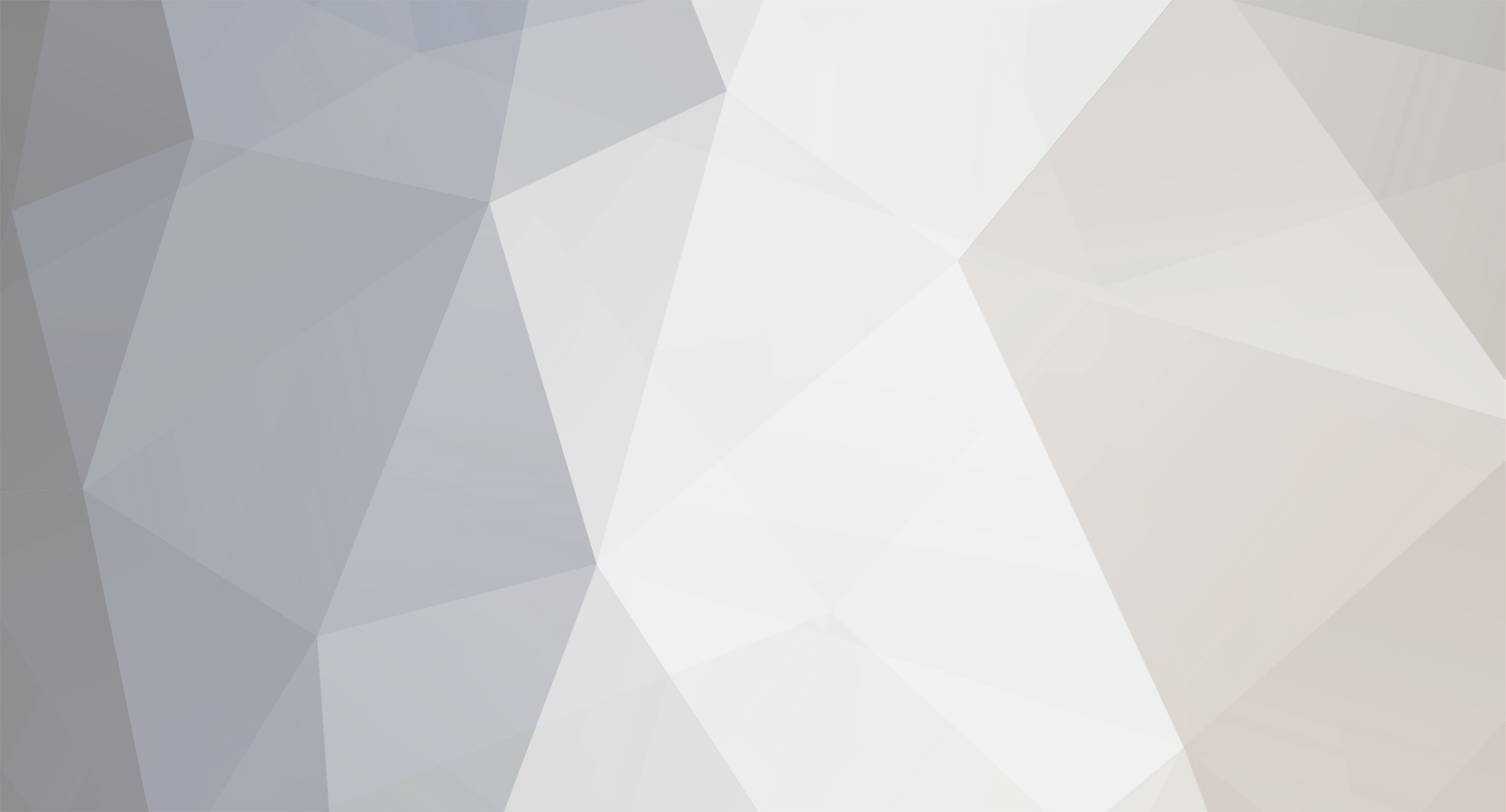
RTurner
Members-
Posts
47 -
Joined
-
Last visited
Never
Content Type
Profiles
Forums
Blogs
Gallery
Everything posted by RTurner
-
Silkscreening isn't necessarily hard, or expensive, but it does take some experience and know-how to get professional results. But nothing that's beyond anyone with a day or two to spare and some scrap to practice on. Silk-screening tips: 1. Keep your artwork as simple as possible. (That is, use sans-serif fonts sized large enough that they'll show through a screen that prints 72dpi, avoid thin lines, don't fool yourself into thinking you can pull-off CMYK type work, the smaller a feature the less detail it should have, the "blockier" the better, use as few colors as possible) 2. Make sure to proof your screen for pinholes. 3. Either use masking-tape or a combination of masking-tape and filler to block-out the edges of your screen (if you have a registration system, don't block out the registration marks, tape them out after your tests). 4. Avoid half-tone work (it's surprisingly hard to get it to turn out right in a silk-screen shop with the proper machinery etc.... Probably next to impossible to do at home without investing $$$) 5. Avoid full-color work. You do not have the proper tools (flash units, registration system...) to make it turn out right, again, this stuff is a pain in a shop, and minor variations in color make these never look quite right. 6. You will often (as in always) have to go back over white or light colors, and it helps with non-white light colors to have a layer of white underneath. 7. Depending on what ink you're using (for panels, an epoxy-based ink that sets with either UV or heat is acceptable) make certain to do a partial cure (while it's lined up) before doing the next color. 8. Print from Lightest to darkest color. 9. When manual silk-screening, get a bead of ink that runs the top width of the screen. With your squeegy lightly pull from top to bottom in a smooth action to "flood" the screen with a layer of ink. Then, from top to bottom, firmly drag the squeegy down in order to push the ink through the screen. You may want to repeat this process another once or twice in order to maker certain there is enough ink on what you're printing. Really, you can make it pretty simple for yourself AS LONG AS you stay with a single dark color on a light background. In which case you can do it with a single screen, in one to two passes (depending on the ink). Oh yeah, most importantly: KEEP WHAT YOU'RE SCREENING ONTO STILL.
-
If panel mount is just as good, how come it's comparatively rare?
-
Silkscreening: Print artwork to transparency. Expose light-sensitive photo-emulsion. Set. Wash the screen. Use screen filler to fill in edges and mistakes. Set again. I know it *sounds* like silkscreening has a low DPI, and... It does, but it's dense enough to reproduce half-tone images, etc... Especially lettering- all it takes is some time in the layout process...
-
Really, I thought one of my friends was putting this guy up to it as a joke. I wasn't even DJing that night. I had my MPC, Mixer, and my effects boxes. It was pretty incredible. One of those horror stories that sticks with me.
-
It's easier, and the components bolt in over the holes you made- usually also hiding common imperfections. Not only that, but if a potentiometer were to go funny (ever owned a stanton DJ mixer?)- it makes replacements a lot easier (assuming you always use header connections- which you do, right?) The only disadvantages are: Sometimes the hardware is a little ugly (like the panel mount MIDI sockets with that aluminum flange)- but these can often times be mounted to the inside of a panel. And yes, there are more wires involved- but again, this actually makes it easier to replace components later when things go wrong and that guy that's been bugging you all night to play "that techno remix of All Along the Watchtower" (true story) pours his cosmopolitan into your main levels fader. I'm not saying that it'll help you that very moment, but at least you'll be able to repair it without desoldering anything (Xytronics desoldering station is a life-saver BTW)...... Anyways- Panel-mount everything you can.
-
Well.... Being a veteran silkscreener (that is, I used to work in a silk-screen print shop) I can tell you that for small runs it will be easier to do it on your own. A lot of shops won't bother with small orders at all (that is, less than 50 pieces), and the ones that do are likely to charge you a righteous set-up fee, and probably charge you to double-check your artwork as well. Doing your own silkscreening is not rocket science. Just remember- use silk screen ink, use an appropriate thread count, for printing on plastics use an epoxy type ink, for your sanity, use a single color, and make sure that it is significantly darker than whatever you're printing on. Actually, the more I think about it, the more I think silkscreening would probably end in disaster 90% of the time for the guy at home. I hear that the decal plus gloss clear-coat looks pretty good.
-
Yeah, the prices are WAY higher than the guy quoted me in the email... So it won't be the best solution for your monome-killer.
-
Yeah, definitely sign me up for some Alps motorpots. Re: Panasonic I spoke with both a Panasonic Rep and someone from their distributor, and sorry... At least in the U.S. there aren't any Panasonic motorpots that exist in regular channels (that is, not hiding in a box in the back of some mom-n-pop electronics store in Idaho).
-
Penny & Giles faders, and an idea for the MidiBox/LC in general
RTurner replied to hædwerkn's topic in MIDIbox HUIs
Bad news regarding the Panasonic motorized slide pots... I talked with one of their reps a while back- they stopped making them. He didn't know why- as they were pretty popular. He got me in contact with the regional distributor whose stock of faders was bought-up buy a couple audio companies immediately after they were discontinued. So you MIGHT be able to find somewhere with a back-stock, but good-luck. ALPs makes the next-cheapest motor-pot at around $25 US (I guess that'd be about $40 AUS or so)... Which is still about 1/3rd the price of anything from P&G... But hella expensive for any mortal.. Robin -
Seriously- I don't think any special contact material would be needed for regular home use. Not only that, but you can clean the contacts with a pencil eraser if they do tarnish, and you usually know when a contact is going (it'll work intermittently for a while before it fails). So unless you were planning on mass-producing something, I don't think it'll be an issue, or if it is, it'll only be an issue every couple years... I'm down for a group order, especially if we can get them to throw in the PCBs. I know that their production volume is going to be at least 1000 pieces, so if we could round-up a couple dozen orders (personally- I could use several of these things building my MPC-killer) I think that would qualify as a bulk order.... So, in case their PCBs are not available, is anyone particularly talented with Eagle??? The way the pad is designed there are score marks to ease in separating the 4x4 silicone pad into 4 groups of 2x2. The pad is 2mm thick in between buttons, so there's no good reason why you couldn't cut it up into as many pieces as you want- though you would probably want to glue 1.5mm thick stand-offs to support the button, and also glue it to the PCB since you'd have one mounting hole per button.. Sorry- The design is for (more or less) square buttons. No mention was made of rounded buttons.. However, the guy I contacted did say that they were working on an enclosure.. But I have no idea what they mean by that. Here's a PDF I quickly made- so that everyone knows what we're dealing with. Sorry if the PDF is a little retarded- acrobat is not my forte'. 4x4_button_array.pdf 4x4_button_array.pdf
-
I was thinking: Etch the appropriate traces, and silk-screen on the contacts using conductive epoxy or some other conductive ink... Yeah... I know.... Regular copper contacts will corrode, and tin will oxidize- which for home use wouldn't be a huge deal (pull out your screwdriver and pencil erasers.). Surely I've poured rubbing alcohol down many a crossfader to get it to perform.. But that wouldn't be acceptable for home use. So.... Does anyone know the likelihood of the silver in conductive epoxy tarnishing? Otherwise: you could use tabs of conductive aluminum tape.... Or use the above mentioned conductive epoxy to mount pads of conductive silicone, etc.... I mean, you're right, it's more than a 2 step process, and I'm fortunate to have a bit of experience silkscreening, but this is still a lot easier to do (and within the means of someone working out of their basement) than to mold their own buttons... robin
-
They are taking care of the hard part. The PCBs are simple in comparison. I suppose this will allow people to choose between a matrix setup and a per-button IO setup...
-
The documentation says that it has a resolution of 128 (I think it can generate that by comparing changes in capacitence in the adjacent... Ummm.. electrodes). 128 isn't great, though just as good as 99% of the midi-able sliders out there, but I don't see why you couldn't have (for example) 2 units stacked lengthwise to create 256 positions and resolve the value in software.... Unless the sensors will interact with each other badly.. Just some thoughts...
-
Just wondering if anyone has tried to use these: http://www.qprox.com/products/qslide_qt411.php I'm asking because it could be a replacement for the co$tly motorfaders from Alps. It could be used as a sort of linear encoder. I know, it uses SPI.
-
Ok, there's both good and bad news... First the good news: They now have a datasheet posted. It can be found at: http://www.sparkfun.com/cgi-bin/phpbb/viewtopic.php?t=3583 The datasheet is a little vague on the size/placement of the conductive silicone, also dimensions are not given for LED pill (I think it's called a pill.... but regardless, I'm refering to the space in the button made for the LED). All the same, I have drafted it up in Autodesk Inventor as an .IPT file if anyone wants it. The bad news: Right now it will be offered as the silicone buttons only. No PCB yet. No enclosure. Having said that: the buttons act the same way as membrane switches; actuating conductor with contacts- so creating your own PCBs won't be that hard. Of course, with the LEDs it will require either a double-sided PCB or two PCBs stacked with through-holes... If any of you do want the .IPT file, I'd be happy to e-mail it to you, but: please excuse me, I'm making the transition from Autocad to Inventor, so the conventions I use may be a little different from what you're used to, especially since I learned architectural drafting and not mechanical- and I ad-libbed the above said vagueries: Pill dimensions (which I know are large enough for a 5mm LED) and Conductive Silicone dimensions. Hopefully by next week I'll have appropriate eagle files with contacts, LEDs, diodes, and header...
-
The monome website says that each button face is .75"x.75" (19.05mm sq)... Not that they would definitely use those dimensions, but I know that development was helped by the monome guys. I dunno, Honestly, I was looking at individual lighted buttons that cost anywhere from $7 to $30US. So one to two dollars a piece seems more than reasonable to me.
-
Spark Fun Electronics will be carrying silicone illuminated buttons based on the Monome design in 1-2 months. 4x4 arrays that will cost between $20 and $30 U.S... !!!! Here's a copy of the email I received: "...We are having the tooling made and should have the first units in 4-6 weeks. We are getting a 4x4 button array with 5mm holes for our tri-color LEDs. The retail price will be in the 20-$30 range but the 16 button pad has been designed so that you can cut it up to 2x2s easily. We are also working on a PCB and plastic frame. Thanks for the inquiry! We are excited to be carrying the pads soon. -Nathan"
-
What about implementing OSC (open sound control) for automapping? I know that some of the Native Instruments programs support it, Max/Msp, as well as some of the cooler boutique-electronics type controllers (Monome, Lemur). Not only that, but since OSC could let you embed midi data within it over some other, faster, interface.
-
I've been looking high and low for these. Let's suppose for a moment that I can't cannibalize one out of a VCR, and that I have to buy it new. It's as if no one makes them. I've considered trying to make one myself... I have a friend with a metal lathe, and I think, with some clever workmanship I could make a pretty cool aluminum jog wheel, with outer ring, out of 3 pieces of turned aluminum, a laser cut piece of plexiglas, a couple ball-bearing joints, a giant nut, some carefully placed epoxy, a couple rubber bands, rotary encoder, and a couple tact switches... But there HAS to be an easier way. I mean, seriously, the approach above would A) take several hours to cut B) require me to purchase a couple un-godly sized pieces of round aluminum stock (which would cost me about $75, but could provide enough jog wheels from here to eternity) C) require me to send off yet another thing to be laser cut. D) use special epoxies to bond aluminum to steel E) find a rotary encoder with an obnoxious shaft length It'd cost me about $100 for the first jog wheel! On the other hand, the second would cost closer to $15 or $20 etc... I'm thinking that jog wheels have a technical name that they'd be sold under. So.... Does anyone know a source for these? Does anyone know what they're actually called? or, if not, does anyone want to buy some really cool hand-made aluminum jog wheels for cost + labor and shipping?
-
I've started a couple designs that will have the front panels cut in plexiglas. It was just Waaaayyyy cheaper than aluminum (about 1/3rd the price). There's a place in my town that'll charge a $20 setup, about $1 per square foot for material, and the actual cutting fee is about another $20-30 on top, comparable work in aluminum would be $120+. Pros: Cheap, can be laser-cut, modifications are easy to do with regular tools, can be back-lit, can be easily silk-screened (with the right ink), comes in a variety of colors and transparencies, can be laser-etched, solvent-welded, and bent with the right tools. Cons: Scratches easily, in order for panels to be rigid they have to be about 6mm thick and thus you have to take that into account with your controllers (slide potentiometers have to have an extra long shaft)...
-
Alright, the good news: at a local computer/electronics store I found a stash of bourns pots that are pretty much everything I need... 10k, 5/8" diameter base, great <ahem> rotational action on the shaft, they're even of the conductive plastic type. I was able to buy a box of 26 for $40! (eat it, mouser) The trade off: the shaft is metal, but it's 1/8th inch in diameter........ were aluminum knobs just never made for 1/8th inch shafts??? Oh well, thanks for the swift replies guys. Robin
-
Does anyone know of any practical reason why one should use potentiometers with metal shafts versus plastic? Are they more prone to breaking? Bending? The reason I ask is: I like the "feel" of Bourns potentiometers, however; the only ones that seem to be reasonably priced have plastic shafts. Even the approx. $3 that mouser wants per potentiometer is a bit steep for me, but, $3 is closer to my price range than the 5+ dollars the others are going for... Thanks, Robin