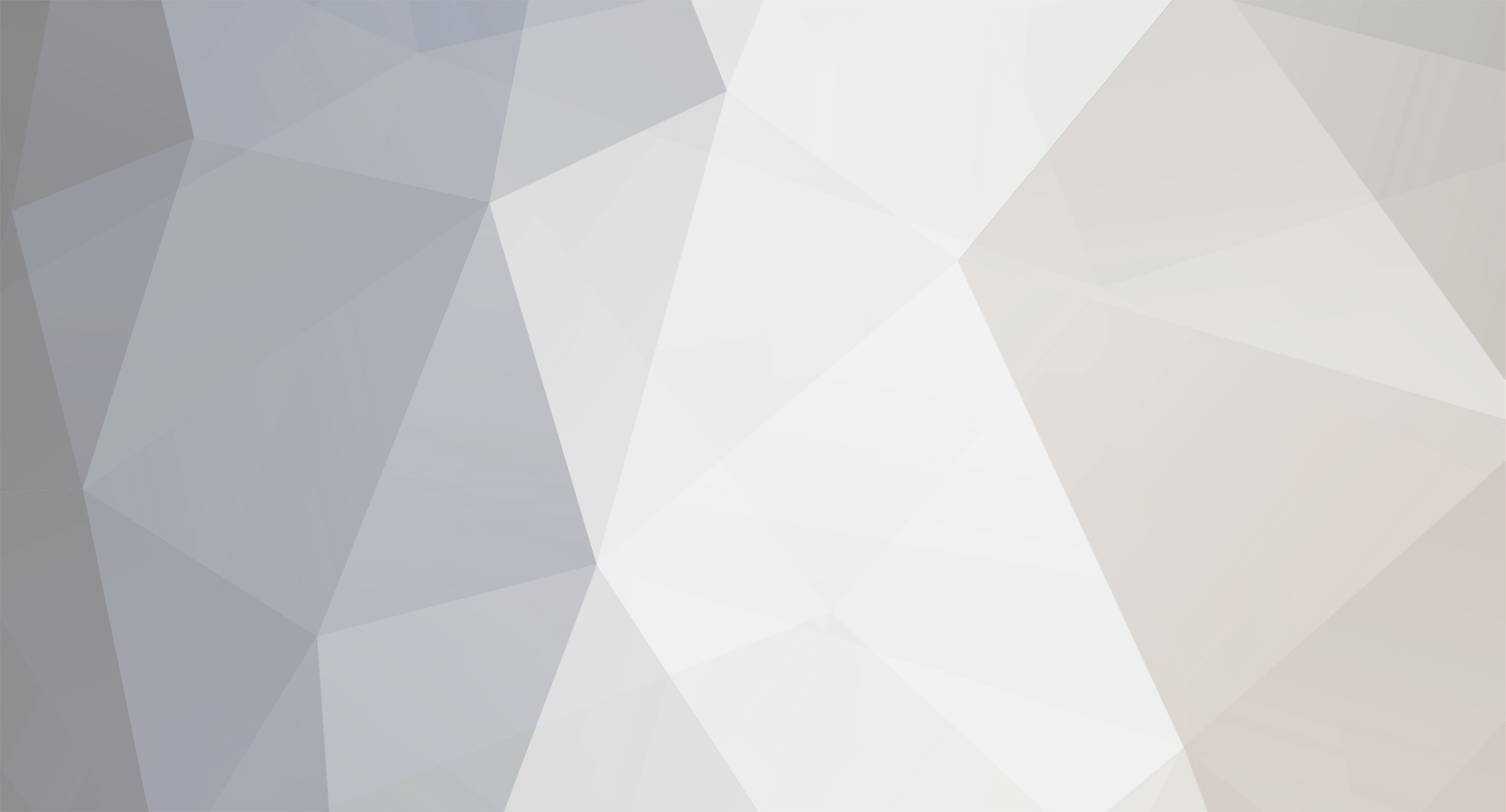
nym
Members-
Posts
31 -
Joined
-
Last visited
Never
Content Type
Profiles
Forums
Blogs
Gallery
Everything posted by nym
-
newer question - suggestions for cureable rubbers for pads?
nym replied to nym's topic in Parts Questions
i have the sensor detail all worked out using CUI sensors - they're particularly nice because tehy have domed surfaces. they're shipping me samples of 2 types right now. using FSRs would drive the cost of this whole operation up probably 150 USD per unit. i'm ordering up some liquid silicon soon. ready to make this thing work again. -
newer question - suggestions for cureable rubbers for pads?
nym replied to nym's topic in Parts Questions
great. i'm probably gonna go for some stuff i found that's got good tear resistability, 28A shore hardness. i'm also gonna make the pads themselves thicker - forat and others did that for the 3000 back in the day and people really liked it. modnar, did you move from the 1k because of the pad issues? i'd love to get you back on the team -
replacing a slide pot with a infared distance sensor in an existing unit
nym replied to nym's topic in Design Concepts
oh sorry, i didn't think other people were necessarily into the mpc thing here at midibox, i tended to think it was more midibox specific and while i'm totally into the whole mb project and plan on someday starting it myself for a custom made controller, i didn't think yall would be interested in some of this stuff. first - http://www7a.biglobe.ne.jp/%7Empc1000/ this guy coded an operating system for the mpc1000 that knocks the PANTS off the existing one. it gives it all of the features of the much more overpriced mpc2500. it also strips it of several really terrible saving bugs. it also knocks off an amp envelope bug, an auto attack bug too. finally, it gives it features not seen ever before in other sampling drum machines - such as control of swing and shift timing using slide potentiometers (and hopefully, someday, distance sensors!) anyway, i started callin this fellow JJ (japanese jenius) because his site gives no name, no identification other than MPC1000. fairly monolithic, so the nickname jj was given. now, if you search mpc1000 and jj you see hundreds of links in a bunch of different languages. he also put PONG on the mpc1000...haha using a distance sensor would let me record slider data (tune, filter, attack, decay, tempo, swing, shift time, sample start, sample end) or midi control changes using my mpc with my face, arms, or any appendage that i can spare while playing drums with both hands. is there anything else i should clarify? -
replacing a slide pot with a infared distance sensor in an existing unit
nym replied to nym's topic in Design Concepts
yo thanks for clearing some of this up. first - what i was getting from japan was information by someone who knows his stuff regarding this 1000. 2nd - i guess i thought this thing was resistive because another sensor i looked at was resistive. 3rd - the whole continuous thing could definitely throw a pin in the gears. i've searched about the sharps here and between that and you post i've realized that it'd be far easier to attempt to do this using a resistive sensor instead of the sharp. this is a project ill think about doing in the future after i finish modding these pads. lot to do, lot to do thanks michael -
new product as in velostat replacing AND mold building for the rubber!!! i've figured out how to do this soooo much more simply found these resistive sensors w/ long life (as long as fsrs) which function the exact same way using this shtuff from japan called inastomer. and get this - remember how much trouble i was having with the mold? these things solve all my problems by BEING ROUNDED THEMSELVES. they actually come with a rounded rubber padlike trigger overtop of the inastomer/active area. so now i'll be putting another layer of rubber (the pad) overtop the domed rubber (the sensor) overtop the metal frame. i'll just be removing the original akai sensors altogether for the "delux" package the akai active area made for all kinds of performance problems and longterm durability issues. this new scheme takes a lot of the load off the damn mold making too, now the mold is much easier to make. my dad's got a workshop, i'm 100% capable of building a mold myself in his basement with the materials he has there. i can even get fancy and do lettering/custom images for people... including graphics or words think about it - pads with hieroglyphics on em...an eyeball, a marijuana leaf, anything all these hip hop thugnerds love. daaaamn, folks - especially modnar so excited about this i'm nearly incontinent as for mr eventoff, it may be that i didn't need to make the contact, but i would love to talk to him anyway to share what i've done and to offer my thanks for his contribution to the world of electronic instruments. i'll definitely post what he has to say. peace guys nym
-
ok! so i'm under way finally with this drum mold. it's 2:20 right now san francisco time and i can't sleep because ideas are flying through my head. i'm getting so excited i can barely function, all i ever talk about anymore is sensors, resistivity, rubber, and midi. so my question is this - what kind of rubber would you recommend for molded drum pads? what shore hardness? anyone got any store preferrably in the US for liquid rubber that would be good? or just some specs/type of rubber to look for? looking for something thatll hold up, not get compressed over time and use, and which will cure nicely. soft is good. i'm thinking maybe even softer than the original mpc drum pads, but i'd like to get some voices on this one from yall thanks again for your help the nymod is under way. between the pad Solution and the Eyepatch (see design) the little mpc is going to explode, and not in the bad way.
-
ok what's up been working on personalizing my mpc1000. this machine is like a fat man in a skinny man's body - the skinny man's skin hurts really bad w/ all the bottled up jellyrolls. essentially, the thing was built not to last, but one bit at a time, i'm fixing these problems. my question is twofold. first, the title question. i'd like to replace one of the slide pots on the left with one of these: http://www.hobbyengineering.com/H1060.html this is an infared distance sensor. essentially it's like the dbeam on an sp808. both sensors, the pot and the infared, are resistive, that is they output different voltages given their own respective environments - slider placement or hand placement. i'd like to be able to control, record, and modulate qlink data using a sharp distance sensor rather than qlink 1, which is the top slide pot. this would still let me control stuff w/ a pot (qlink 2) but also have the more dramatic looking and natural feeling sweep of the hand. the infared reads from 4 to 11.5 cm. that's a convenient, comfortable distance. i will hopefully put it into a place where it could be triggered by my head - as i play my machine, i could lean in and modulate a filter sweep with it. so a couple questions. first, since both are resistive sensors, is it reasonable to think i could simply swap em out? this is a really preliminary question since i know i havent given you the specs on the qlink - i'm working on getting that from a source in japan - but what do i need to know in order to match up the sensors so i can swap em? has anyone had any experience with these infareds before? i played with the one on the sp808 and while some people found that it was clumsy, i was able to get reproduceable and enjoyable effects by using it. it was one thing to do it in realtime, but to be able to record one's smooth hand movement makes my mouth water. 2nd question - much more simple. all of the buttons you see on the left and right are simple switches. they all make a clicking sound when pressed upon. this is not the problem - the issue is repeatability. after 2 years, a couple of these buttons are going bad. akai repairs sell these buttons for like 8 bucks a pop. i think i could do better. what are some switches that could work and are known to last a long time? 2nd, are there switches that one doesn't need to necessarily PUSH in order to triggeR? i could live with a push switch ala the ones that are already on there, but only if they had a long lifespan. ideally, however, i'd like to be able to simply brush my hand against the mpc button and with a light touch trigger the button. however, lifespan of the button beats the light press thing. anyone got good buttons to suggest? thanks for your help and support. peace nym
-
i've made significant ground on my own front as well. soon to be trying 2 new products which might make things easier i actually got in touch with Frank Eventoff, guy who invented the Interlink FSR and coordinated their use w/ roger linn in the original mpcs. very nice guy, i actually called him at home and got his wife, who was kind enough to give my cell number to him. we had a pleasant chat, dude knows his stuff. i'd love to work for him someday.
-
measurements (tell me if more are needed) 1 pad (the visible surface, not the factory lip: 22 mm tall by 30 wide. individual sensor (copper active area): 13 by 13 mm sensor bank: 150 mm by 118 mm individual sensor rectangle: 37 mm wide, 29.5 mm tall. space between sensor board and faceplate: just over 2 mm
-
as for the no pressure, in my design i have it resting against the active area at all times, and it doesn't trigger until you give it a little pressure - and i'm talking about the SLIGHTEST pressure, like brushing it gives you a contact. this could potentially give a problem, if your design isn't tight enough that there is a "bounce" to it and that causes tiny pressure on the velostat. however, if it's secure, then there's nothing to worry about and you have yourself some REALLY sensitive pads. i'm dealing with copper coil active areas that require a material to make the connection overtop between the 2 coils. the velostat suits that purpose. (mpc1000). the sampler records notes in (who woulda guessed) midi, from 1-127. pressing down the pad in the slightest way gives a contact of 1-10. an appropriately hard hit gives 127. it's perfect for pad applications, not to mention other cool things haha like preventing alien abduction...
-
will do. sorry for the delay. i'll try to get it out before the 6th, when i'll be shippin out to san francisco.
-
modnar that composition looks REALLY good, but according to frontpanel it'd cost me close to 150...i'd be willing to make that kind of money appear but it might take a while. i will get you measurements, got to run and get myself a measuring tape that doesn't measure in ass backwards notation checkin out sparkfun right now. i remember seeing a monome video and waking up with foamed saliva around my mouth, with one leg twisted underneath my body. goddamn pleasure seizures.
-
yo so here i am now. this is a trial run of using 2 faceplates like you said. imagine them on top of one another. one goes over 2, 2 provides the dome. they're the same size of course, just different zoomed screenshots
-
i'd scoff if it was 20 usd, this stuff requires no shipping considerations whatsoever
-
and clear copper, so you could see the -- nah, i've taken this too far.
-
wtf 80 dollars? that's rediculous. when i order more, wilba, i could simply put some into an envelope and mail it that way for considerably less than 80 dollars, ie a couple more stamps than usual. it's paper thin, i don't get why the hell they're charging that much money.
-
oh absolutely. i've done that by just securing down the existing 16 boards to a central sheet. they ain't going anywhere, but i'd love to someday actually have my solid pcb in there, it'd be very cool, esp if i got some clear silicon to be the pads...haha but i'm getting ahead of myself again.
-
you mean the sensor board? what do you think you'd consider changing if you could? broader copper coils as i was blabbing on about? yeah man thanks, this looks great too.
-
and let me say - you've been a major help all along, since day 1 on this whole thing. modifying your gear is exciting as hell, man, i can't BELIEVE i'm the only person i know of doing this to their 1k.
-
yo back again, modnar. this Front Panel thing is ReaLLY cool, i like the little program, it's awesome for custom stuff. this is a brilliant find. my question is this - since i'm figuring out this pgm, i want to at least design a domed underside pad sheet, ala the original design, rather than expand the existing sensors. this program makes it easier than i had thought, probably easier than the conductive ink idea. SO you're able to make "cavities," indented shapes. this is how i'm making the pad (1 rectangular cavity that's a quarter inch deep) and then additional cavities overtop the first - ie, the dome, roughly 1/32 deep. pardon my use of this idiotic measuring system, i regret that i only have a so called "standard" measuring tape at my immediate disposal. NOW my question is this - are these depths cumulative? i'll explain further in case i'm not being clear. my steps: 1 - make rectangle cavity 2 - set itsdepth at 1/4 deep. 3 - make oval cavity IN rectangle cavity for dome. 4 - QUESTION: set depth of dome to 1/32 deep, OR 1/32 + 1/4 deep? is it already taking the preexisting cavity into consideration? if you don't know this, it looks like they have a number i could easily call. thanks man, this is going really well... nym
-
check it out cheap as hell, really useful. http://www.blockemf.com/catalog/advanced_search_result.php?search_in_description=1&keywords=velostat&x=0&y=0
-
appropriately named for me :o
-
at this point i'm afraid the topic has changed from "parts" to "design" and i'm afraid it may be in the wrong subforum, apologies to the mods
-
"domed surface" i have figured out that it's not area of contact that registers a harder hit. the domed surface's purpose is because of this:the active area is about the size of your thumbnail, a little smaller. the dome is there so that when you hit the corner of the mpc pad, the dome moves down and hits the contact area. this presents a problem because i don't want to have an air gap in between the pad rubber and the sensor. this implies a moving part, and is not ideal for this given sensor setup. it works for interlink style FSRs but NOT for this unlaminated sensor technique. however, w/out a domed surface, a corner hit of the mpc pad won't make a trigger - you have to make a hit solidly in the middle of the goddamn pad. it works well, but it creates a smaller target area. people may not like this, but i don't think i'm willing as of now to make a domed underside because it's an inappropriate design... UNLESS the active area of the sensor is expanded...which opens my next question. i want to continue this spiral so that there's more of an active area - with a carbon laden ink. i've been reading about this stuff - you paint it on w/ a little brush and then when it cures you scrape off the thin insulative surface overtop of it to bare the conductive. this would provide a low-conductive expansion so that even a corner hit would make some contact. it's either this or build my own new copper coil thing, but that might be a little much, i'm just looking to get back to 150% working condition. this may be more for my own personal design, not for people who want a prefabbed technique. i don't expect this to be something that people will do on their own. i'm having a feeling i'm gonna have to start a little forat style thing where people send me their samplers and i do it all myself...might just be easier/safer for them...but who knows.
-
i ordered a sheet of stuff at 45A one time and it was incredibly flimsy...very easily stressed and didn't spring back to its original shape. i may have to adapt my order though if you think 50 is too hard, because i ordered something at a little less than 1/16th thick at 60 A. this i had planned to put underneath the metal frame of the mpc and call it a day. no raised pad surface at all. this would be cost effective, but i don't know how peopel would react to not having "THOSE PADS" even if the end result is the same however, i really should bite the bullet and look into the whole molding/silicon process. how much more expensive would it be? i'd really have to hike up the price this way. then again i could offer either or. i'd probably prefer the latter though just because i'm more used to it. how much is self-curable silicon? as for what you said before - the idea of 1 pad sheet instead of 16 individual bits. this is a must - or at least 4 equal sized squares/strips. having individual pads is one of the worst ideas i have ever heard of. here's the other question - the thinnest part of the silicon (the "Sheet" part, the part that connects the pads to each other and fits under the frame grid) is gonna have to be about 1/16th of an inch thick. that's pretty small. does that run a risk of tearing? granted, once it's in there there's not gonna be much that really could tear it save some lunatic giving it a grapple with his teeth, but you see my concern. time to look into frontpanel xpress.