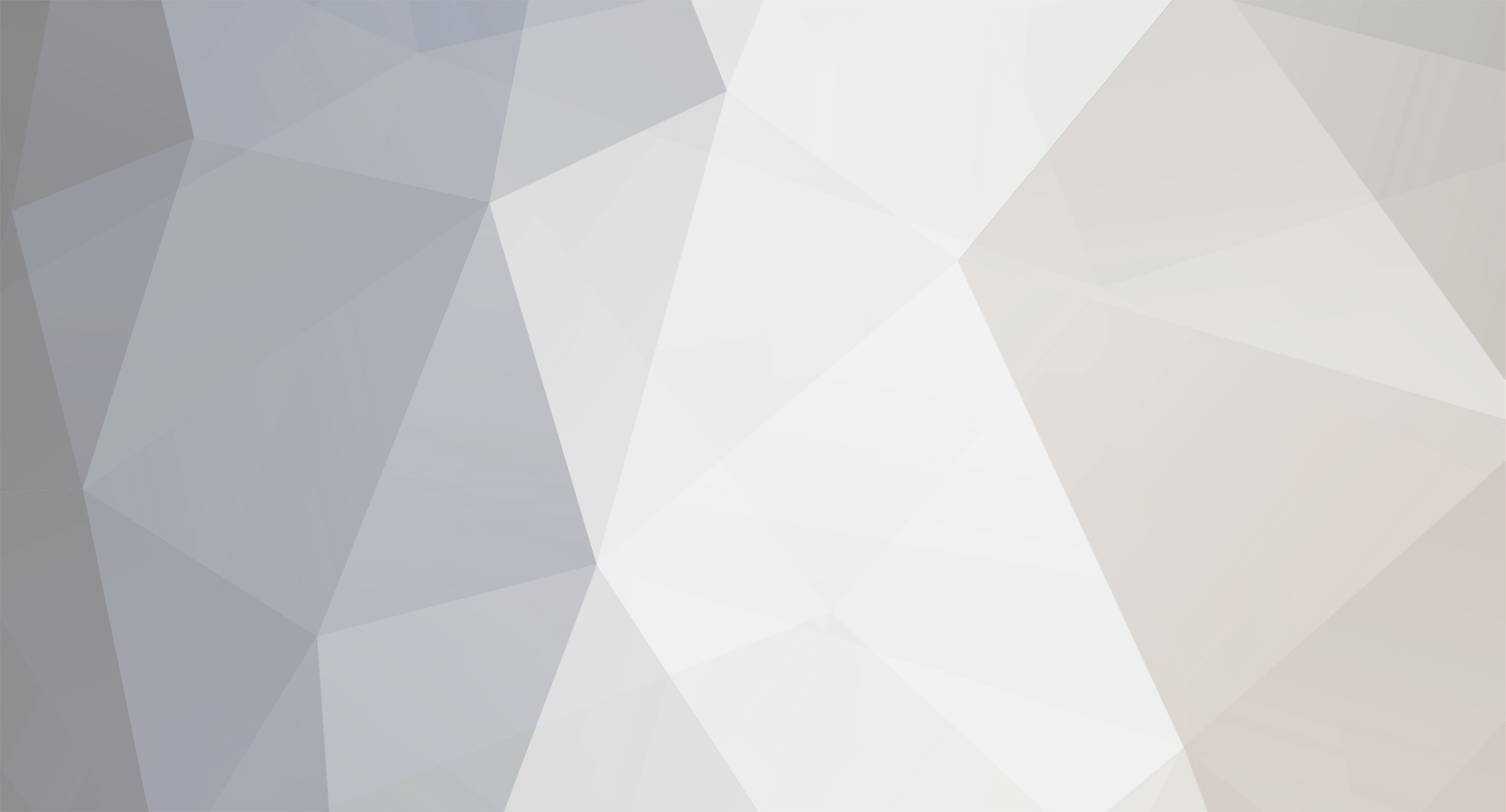
Zam
-
Posts
625 -
Joined
-
Last visited
-
Days Won
26
Content Type
Profiles
Forums
Blogs
Gallery
Posts posted by Zam
-
-
3 hours ago, TK. said:
What would be interesting: what happens if you start MIOS Studio from a terminal:
I try
open -a MIOS_Studio
same result...
Best
Zam
-
Hi Thorsten
Long time, hope you get well !
Crash before opening anything on my Air M1
I'll send the report in PM if that help.
Best
Zam
-
23 hours ago, ksir said:
doesn't seem to work
IIRC this is a global definition, not an event definition !
You have to put it only once at the beginning of your .NGC config file, it will set all SRIO to the specified value.
Check to be sure but probably max value (65535) is way to much, like 30sec for 32 shift register ! that's a long time before being able to push a button again.
You should be able to monitor the bouncing time of the button (via midi or debug), maybe there is more than one bounce actually, you'll see.
Set the debounce time about twice that to be safe, or whatever higher possible value without feeling some requested fast push don't work.
-
From NG user manual, .NGC config, SRIO section
debounce_cycles=<0..65535> This command allows to enable a debouncing mechanism for digital inputs (buttons). The number specifies the dead time in SRIO cycles at which button events will be rejected.
The time of a SRIO cycle depends on the num_sr configuration, typically it's around 420 uS for 32 SRs, which means that with debounce_cycles=20 the debouncing dead time is 8.4 mS. -
Hi
Long time I don't play with NG config, but It should be possible with enc_mode=Inc41_Dec3F , combined with fwd to 2 sender and conditional filtering, something like if_equal=0x41 send note A, and if_equal=0x3F send note B ?
-
1
-
-
15 hours ago, Phatline said:
by RM you meen a Ringmodulator-coil?
Nope
RM is a standardised coil assembly, with pcb mount coil former.
-
I'll be in the need within 6/12 month I'll say.
Don't know yet if I'll use subcontractor, or if I buy or build a winding machine.
-
Hey Mike
Excellent project !
I might be interested as I'll need to wind RM coil soon
Dose your code or parameter setting offer multi layer winding ? going back and forth within a coil former length ?
Best
Zam
-
Yes you usually need a metallized knob to make the touch detection usable !!!
-
1
-
-
2 hours ago, FantomXR said:
How could "if_" help here?
it's a conditional, it will activate the event according to value
don't remember precise form, I don't write NGC since years now, but something like if_less=37, your receiver will forward only data from 0 to 36
-
Hi Chris
IIRC range= is not a split but a scale function, so range=0:36 change value 0-->0, 127-->36 and linear ponderation in-between.
maybe try with conditional function, if_=
Cheers
Zam
-
Hi
Long time I don't talk here
Your P&G have big (coreless ?) motor, I suspect you need way more power than MF_NG is able to offer, but I don't remember precisely what onboard reg offer, 10V 1A ?
That's probably why it's not smooth. For those motors you probably need 24V, with probably more than 1A in stall condition...you need good protection/limiter otherwise you'll blow drivers
About PWM "printer" noise, it's more or less intrinsic.
There is a lot of PWM motor driver, you can probably test some others and have better result ?
Side question, is't those Amek series loaded with VCA fader ?
Best
Zam
-
hello
you need to define MF events for each fader and associated midi event, which is different from the (fader) module parameter
this is the partial NG template for motor fader
################################################################################ # Motorfaders ################################################################################ # we've a single MBHP_MF_NG module with 8 motorfaders # It has to be configured for Motormix protocol! MF n=1 enabled=1 midi_in_port=IN3 midi_out_port=OUT3 chn=1 ts_first_button_id=2001 config_port=USB3 # on motorfader movements EVENT_MF id= 1 type=PitchBend chn= 1 range=0:16383 EVENT_MF id= 2 type=PitchBend chn= 2 range=0:16383 EVENT_MF id= 3 type=PitchBend chn= 3 range=0:16383 EVENT_MF id= 4 type=PitchBend chn= 4 range=0:16383 EVENT_MF id= 5 type=PitchBend chn= 5 range=0:16383 EVENT_MF id= 6 type=PitchBend chn= 6 range=0:16383 EVENT_MF id= 7 type=PitchBend chn= 7 range=0:16383 EVENT_MF id= 8 type=PitchBend chn= 8 range=0:16383 # on touchsensor event (first id has been specified in the MF configuration above) EVENT_BUTTON id= 2001 type=NoteOn chn= 1 key=0x68 range=0:127 EVENT_BUTTON id= 2002 type=NoteOn chn= 1 key=0x69 range=0:127 EVENT_BUTTON id= 2003 type=NoteOn chn= 1 key=0x70 range=0:127 EVENT_BUTTON id= 2004 type=NoteOn chn= 1 key=0x71 range=0:127 EVENT_BUTTON id= 2005 type=NoteOn chn= 1 key=0x72 range=0:127 EVENT_BUTTON id= 2006 type=NoteOn chn= 1 key=0x73 range=0:127 EVENT_BUTTON id= 2007 type=NoteOn chn= 1 key=0x74 range=0:127 EVENT_BUTTON id= 2008 type=NoteOn chn= 1 key=0x75 range=0:127
best
Zam
-
Hello
Obviously you have access to the core and NG files, so the first step seem fine.
What say the debug mode ?
edit: I just read again your post... you say your .NGC is called "Hello"
without specific "load" command (you'll see later) MBNG at start-up ONLY load config files called DEFAULT.NGC and DEFAULT.NGR
just rename your .NGC
Best
Zam
-
Hello
Can't say for MIDIO128... but for MB_NG it's in the .ngc parameter file.
Best
Zam
-
Hello Thomas
Look promising !
Best
Zam
-
17 hours ago, totoRaymond said:
If I remember well, you're problem with PWM was related to EMI leaking into the analog circuitry, not the actual physical noise of the fader. Am I right?
It was both,
EMI not acceptable regarding technical performance I requested then, with that particularity that I have low level audio signal just across the digital circuit, which is not a question/issue for 99% of pple using MF_NG.
As acoustic noise that can't match the quality standard at user side I was searching for, in a quiet as possible "high-end" control room I can't work with a bunch of printer like sound, unfortunately a fader automation is not a tool that you can put in the machine room
In a way both noises are linked.
Best
Zam
-
Hey Thomas
As you notice I take another route long time ago, I'm not able to help you much about PWM handling
I think I publish all my tries around PWM by that time, and there is probably other options to test today, including increasing frequency of the PWM (over audio range). IIRC mios8 on the pic can't do this ?
Do you know how is handled the motor in the D-com ?
Best
Zam
-
Hello
On 20/08/2020 at 0:11 PM, totoRaymond said:I'm pretty sure i'm doing something wrong here, but i can't figure out what...
I'm not sure you do wrong, this is probably intrinsically related to PWM driver
Best
Zam
-
Just now, totoRaymond said:
Now that you mention it, the second ref on the motor might refer to this
Nice catch !
Whit this I think we can definitely say this is a digital encoder implementation around a P&G "blank" fader
The fader is just use as mechanical device to translate rotary to linear actuation
We have here a 256 steps/turn version. Can't say how many steps it translate to the linear movement, this is defined by pulleys/axis diameter ratio, but we can expect more than one motor turn for a fader full travel.
Best
Zam
-
Hello
6 wire to the motor...should be a step/rotary counter...
1 hour ago, totoRaymond said:Now the four others must be 100%V, 0%V, Wiper, and Touch sense. In that order IF P&G kept the same when changing design.
The OP just say there is no resistive element in the fader, and you can see there is no wire going to the fader !
You won't find any taper resistance here nor touch sens.
This is probably a rotary encoder/counter technology embeded in the motor
Stagetec do broadcast console, I suppose there is no automation on it but recall and fader flip function where the encoder is enough to send fader at visual position (this is a remote)
As there is probably a calibration routine at startup with such advanced digital desk, the drift or miss count of motor turn for precise fader position is not a issue.
As is it seem complicated to use this with midibox HW
What you can try maybe is wiring pin 3-4 and 5-6 (assuming 1-2 is motor...) to a DIN in encoder mode
and at least know how many count you have for a full travel, that data will give you fader accuracy and position.
Then find a solution to use this data in place of analog input (from a resistive passive element) to handle data that will tell the motor what to do.
Best
Zam
-
Off topic...
J'avais oublié... ca pique fort quand même
Zam
-
Hello
AINSER modules have pinrange option which is basically used to add dead band at start and end of a pot. It can be considered as a threshold if you set value high.
MAP definitions can also be used to achieve threshold functions.
There is sensor mode too, but not used to it, so you have to look by yourself
Best
-
Hello Micha
To understand the whole mechanism we need to know what do section 1 as you call it at the end of the section 2...
Also your sender 4043 have key definition which is not relevant due to type=meta
What about the buttons that select banks ? Do they forward to receiver 4042/4043 ?
Best
Zam
MIOS Studio 2.4.9 re-release for Macs with "Apple Silicon"
in MIDIbox Tools & MIOS Studio
Posted
In practice It's a non issue for me as this computer is not the main one I use with midibox HW, also the previous version (non apple silicon) run fine on the M1 last time I check and communicate/UL data to a core.
Basically just see your initial post and download the app to see, and then give feedback.
Best
Zam