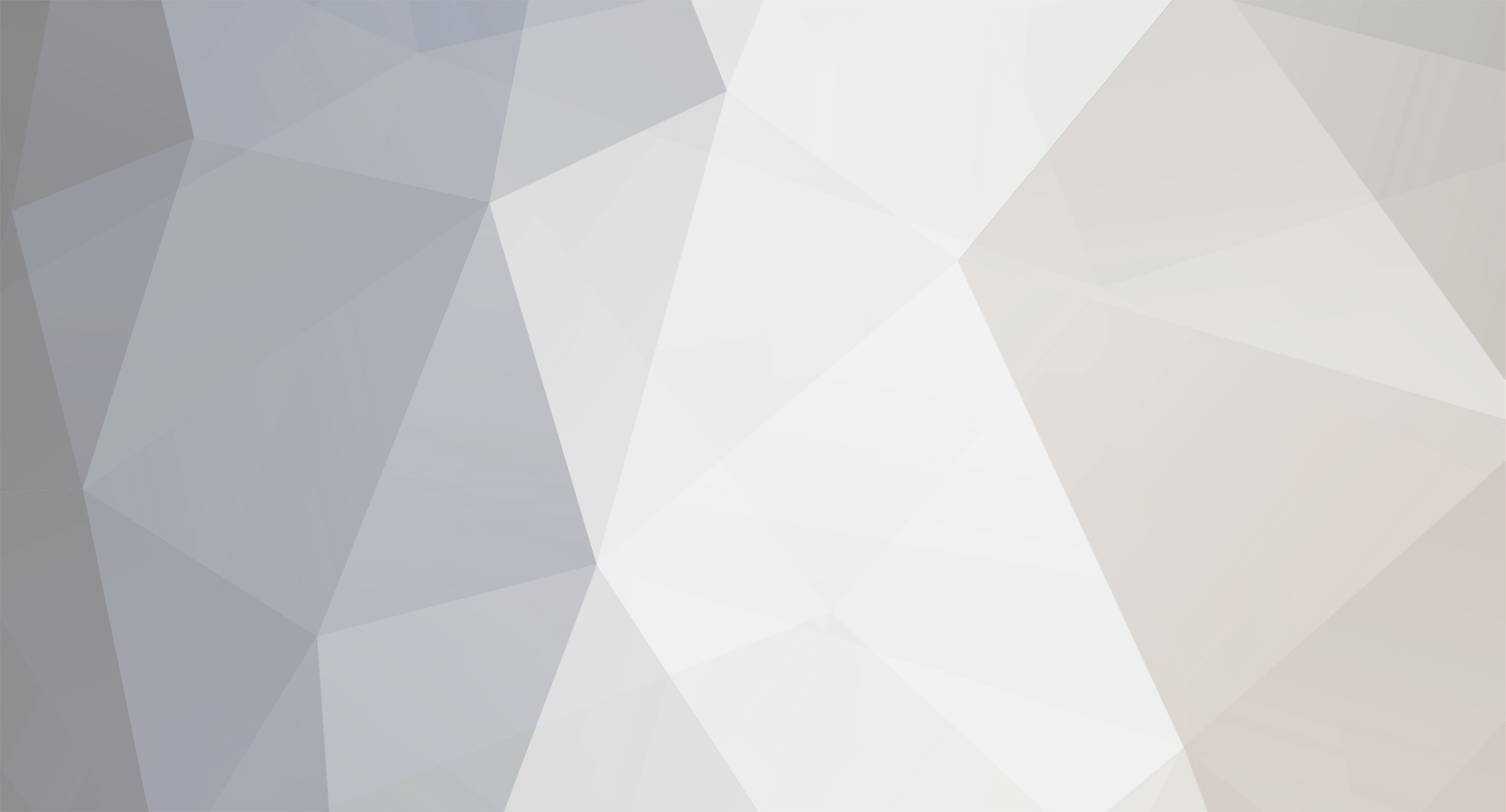
Zam
Members-
Posts
625 -
Joined
-
Last visited
-
Days Won
26
Zam last won the day on May 16 2023
Zam had the most liked content!
Recent Profile Visitors
2,712 profile views
Zam's Achievements

MIDIbox Guru (4/4)
38
Reputation
-
MIOS Studio 2.4.9 re-release for Macs with "Apple Silicon"
Zam replied to TK.'s topic in MIDIbox Tools & MIOS Studio
In practice It's a non issue for me as this computer is not the main one I use with midibox HW, also the previous version (non apple silicon) run fine on the M1 last time I check and communicate/UL data to a core. Basically just see your initial post and download the app to see, and then give feedback. Best Zam -
MIOS Studio 2.4.9 re-release for Macs with "Apple Silicon"
Zam replied to TK.'s topic in MIDIbox Tools & MIOS Studio
I try open -a MIOS_Studio same result... Best Zam -
MIOS Studio 2.4.9 re-release for Macs with "Apple Silicon"
Zam replied to TK.'s topic in MIDIbox Tools & MIOS Studio
Hi Thorsten Long time, hope you get well ! Crash before opening anything on my Air M1 I'll send the report in PM if that help. Best Zam -
IIRC this is a global definition, not an event definition ! You have to put it only once at the beginning of your .NGC config file, it will set all SRIO to the specified value. Check to be sure but probably max value (65535) is way to much, like 30sec for 32 shift register ! that's a long time before being able to push a button again. You should be able to monitor the bouncing time of the button (via midi or debug), maybe there is more than one bounce actually, you'll see. Set the debounce time about twice that to be safe, or whatever higher possible value without feeling some requested fast push don't work.
-
From NG user manual, .NGC config, SRIO section debounce_cycles=<0..65535> This command allows to enable a debouncing mechanism for digital inputs (buttons). The number specifies the dead time in SRIO cycles at which button events will be rejected. The time of a SRIO cycle depends on the num_sr configuration, typically it's around 420 uS for 32 SRs, which means that with debounce_cycles=20 the debouncing dead time is 8.4 mS.
-
Hi Long time I don't play with NG config, but It should be possible with enc_mode=Inc41_Dec3F , combined with fwd to 2 sender and conditional filtering, something like if_equal=0x41 send note A, and if_equal=0x3F send note B ?
-
Coil Winder - MIOS Tesla-Coil winding machine
Zam replied to Phatline's topic in MIDIbox User Projects
Nope RM is a standardised coil assembly, with pcb mount coil former. https://www.tdk-electronics.tdk.com/en/529410/products/product-catalog/ferrites-and-accessories/rm-cores-and-accessories -
Coil Winder - MIOS Tesla-Coil winding machine
Zam replied to Phatline's topic in MIDIbox User Projects
I'll be in the need within 6/12 month I'll say. Don't know yet if I'll use subcontractor, or if I buy or build a winding machine. -
Coil Winder - MIOS Tesla-Coil winding machine
Zam replied to Phatline's topic in MIDIbox User Projects
Hey Mike Excellent project ! I might be interested as I'll need to wind RM coil soon Dose your code or parameter setting offer multi layer winding ? going back and forth within a coil former length ? Best Zam -
Yes you usually need a metallized knob to make the touch detection usable !!!
-
it's a conditional, it will activate the event according to value don't remember precise form, I don't write NGC since years now, but something like if_less=37, your receiver will forward only data from 0 to 36
-
Hi Chris IIRC range= is not a split but a scale function, so range=0:36 change value 0-->0, 127-->36 and linear ponderation in-between. maybe try with conditional function, if_= Cheers Zam
-
Hi Long time I don't talk here Your P&G have big (coreless ?) motor, I suspect you need way more power than MF_NG is able to offer, but I don't remember precisely what onboard reg offer, 10V 1A ? That's probably why it's not smooth. For those motors you probably need 24V, with probably more than 1A in stall condition...you need good protection/limiter otherwise you'll blow drivers About PWM "printer" noise, it's more or less intrinsic. There is a lot of PWM motor driver, you can probably test some others and have better result ? Side question, is't those Amek series loaded with VCA fader ? Best Zam
-
hello you need to define MF events for each fader and associated midi event, which is different from the (fader) module parameter this is the partial NG template for motor fader ################################################################################ # Motorfaders ################################################################################ # we've a single MBHP_MF_NG module with 8 motorfaders # It has to be configured for Motormix protocol! MF n=1 enabled=1 midi_in_port=IN3 midi_out_port=OUT3 chn=1 ts_first_button_id=2001 config_port=USB3 # on motorfader movements EVENT_MF id= 1 type=PitchBend chn= 1 range=0:16383 EVENT_MF id= 2 type=PitchBend chn= 2 range=0:16383 EVENT_MF id= 3 type=PitchBend chn= 3 range=0:16383 EVENT_MF id= 4 type=PitchBend chn= 4 range=0:16383 EVENT_MF id= 5 type=PitchBend chn= 5 range=0:16383 EVENT_MF id= 6 type=PitchBend chn= 6 range=0:16383 EVENT_MF id= 7 type=PitchBend chn= 7 range=0:16383 EVENT_MF id= 8 type=PitchBend chn= 8 range=0:16383 # on touchsensor event (first id has been specified in the MF configuration above) EVENT_BUTTON id= 2001 type=NoteOn chn= 1 key=0x68 range=0:127 EVENT_BUTTON id= 2002 type=NoteOn chn= 1 key=0x69 range=0:127 EVENT_BUTTON id= 2003 type=NoteOn chn= 1 key=0x70 range=0:127 EVENT_BUTTON id= 2004 type=NoteOn chn= 1 key=0x71 range=0:127 EVENT_BUTTON id= 2005 type=NoteOn chn= 1 key=0x72 range=0:127 EVENT_BUTTON id= 2006 type=NoteOn chn= 1 key=0x73 range=0:127 EVENT_BUTTON id= 2007 type=NoteOn chn= 1 key=0x74 range=0:127 EVENT_BUTTON id= 2008 type=NoteOn chn= 1 key=0x75 range=0:127 best Zam
-
Hello Obviously you have access to the core and NG files, so the first step seem fine. What say the debug mode ? edit: I just read again your post... you say your .NGC is called "Hello" without specific "load" command (you'll see later) MBNG at start-up ONLY load config files called DEFAULT.NGC and DEFAULT.NGR just rename your .NGC Best Zam