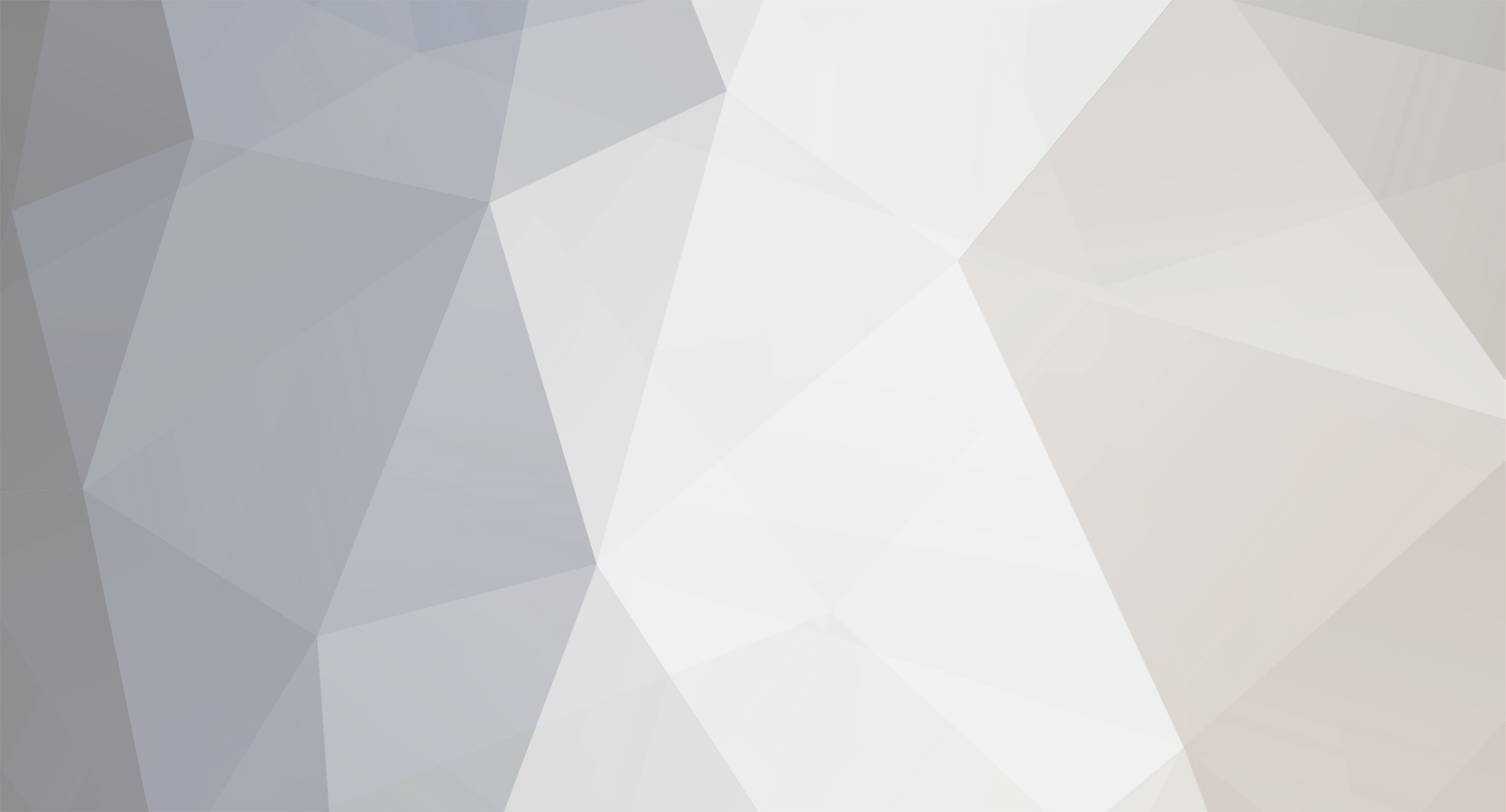
Artesia
Members-
Posts
571 -
Joined
-
Last visited
Content Type
Profiles
Forums
Blogs
Gallery
Everything posted by Artesia
-
artesia - the 'masked sandwich holder' ...now i am puzzled ...unless thats a reference to using a sandwich toaster to heat the boards (which incidentally seems to be the numero uno way to avoid user induced toner smudge ;) ) hmm that stuff sounds deadly, something tells me that my paving slabs arent going to like me... as for what to put something that deadly in, is a plastic storage box really giong to cut it ;) ..hmm definately tong time tho.
-
Indeed, tho reading about these things & actually getting it to work.. is two sepperate things. Maybe different setups (printers, toner, paper, heating methods, interpritations, patience) all give different results and some setups are more more finicky than others to get working usably. Mine certainly seemed to be more picky, than the many dozens i read about before trying myself. And figured that with myself having such a headache with it; that i'd document what i did; hoping that someone else would benifit :) Also finding some of the papers and supplies listed by american (and some european) sites ..are impossible to find under the quoted branding in the UK ...so noting which one seemed to work ok (and how); looked like filling a hole in the information out there :) Fibreglass ...well fibreglass is generally higher quality & more durable (but costs more)
-
Hi, (Consider this a sorta newbie'ish tutorial to DIY PCB's, using the well known Laser printer method ...and a little run-through of my experiences along the way...) I finally decided to have a crack at making DIY pcbs ...as i really need to be able to fab custom ones for project development.. and also i was having difficulty getting some of the MIOS boards :/ :) Well, anyways.. after a little research, i decided to give the Laser Printer toner transfer method a go; and eventually i got it working, after much swearing, unsuitable papers & general experimentation. I eventually found fujifilm 180gsm glossy ** (2 star) inkjet paper (N073170A / BAR: 5036321051242) to be useable with my samsung clp-500 colour laser printer. Whereas photomatt, plain paper, Tracing paper, magazine paper, Rex Glossy paper & card.. where unsatisfactory to useless. Heres a method i found to work, to see more Errata; on account of where things went wrong.. see the end of this post. The Midibox logo on copper :) My first, er... very scruffy; sucessful pcb. (...Honest, the more recent ones look amazing ;) (more pictures to follow, maybe...) First set the printer to thick card setting. (as on standard mode it runs through too fast and too hot, resulting in blistered, peeled & missing toner) Chop the pcb sections to size needed, use fine wet and dry to prepare surface in a circular motion.. or use a 'sponge' sanding block as i did. Get a good shine on it & remove any marks ...to allow for proper toner adheasion & avoid blotchy etching :) Then print design onto fujifilm photogloss paper, cut out design and tape to bottom of pcb with masking tape; completely enclose the pcb with tape (to stop water getting in too quick & lifting the mask, later on) ...Then either use a closthes iron on hottest setting, or do as i did.. place in a smooth surface sandwich toaster (preferably one you dont plan to eat from !) for not much more or less than 1 min; with afew sheets of card below to prevent overheating the non pcb side ...press down hard and quick, until time up. Drop streight into a tub of cold water.. leave for 5-10 mins. When ready (tends to blister a little & show tracks through paper and tape) then slowly and carefully peel off masking tape at an angle close to the board (to prevent lifting the print). Carefully remove remaining paper, weather damp or not.. it should have transferred all of its toner, if done properly anyways. gently roll off remaining flecks of paper with fingers. Dry & check for broken / missing tracks.. if not major, draw them in by hand with a ohp permanent marker pen (or similar). Then dunk in hot (35-65c) ferric cloride solution for 5-10 mins, swishing about until etched ! ..when you cant see any remaining copper, its done ..volia ! ...rise board and sand off & drill with small bit & dremmel for use :) Some notes: * Toner/black needs to go where you want copper to remain on pcb. * make sure that the pcb pattern is mirrored the right way for proper pcb construction, the print should appear on the paper, as if it was the pcb itself... and you where looking through the top of the component side, down onto the tracks. If its applyed incorrectly, you will have your pcb traces on component side ! * Apparently original manifacturers toner works more reliably than 'compatable' stuff. * this -Will Not- work with inkjet printers, although here: http://techref.massmind.org/techref/pcb/etch/directinkjetresist.htm on the net, is a project to turn standard inkjet printers into direct mask to pcb printers, tho you might not fancy that much diy :) Errata: * Waxy label backing (ie: avery) works in a fashon, however it always smudges and blurs a little ..use in an emergency i guess. * Plain paper / card Does not work, too much fibre bonding to toner; peels poorly. * Photo matt is similar to plain paper.. results not been useable; tho i hear epsons own brand works (will try for fun). * Tracing paper will not pick up in printer. * Magazine pages smuge toner, stick to pcb & leave many patchy sections. * Cheap, Glossy Photo papers with a high plastic content (IE: rex office (my epson inkjet hates it too!)) does not give up toner easily & is by far the worst for sticking to the pcb board ..impossible to work with. * Make sure you use a non plastic based tape to wrap up boards.. otherwise everything will get toxic smelly and sticky ! use Fiberous, paper based masking tape. * Make sure masking tape completely encoloses the pcb & paper.. found this to be imperitive to good results. It seems to slow down the takeup of water, which seems to prevent the toner lifting & makes paper removal much easier ..as the masking tape glue seems to soak through the paper & bond to it more strongly than the toner did. Allowing almost all of it to be removed in one go. Pick away remaining bits carefully and all should be fine. Note that some bits maybe dry, however should lift fine ..and youll find that they should have transferred their toner to the board :) * Heating the pcb + paper for too short a time (30 secs as per tests) ..does not allow for complete transfer of toner.. results useless. Heated for 3-5 mins upwards seemed to burn & brittleify the toner, resulting in flaking & smudgeing. Heating the toner for 1 min seems to provide the best results, with complete transfer if boards cleaned properly & fast heavy application of pressure used. * trying to heat more than one sepperate board at a time may result in uneven pressure & poor Toner transfer ! * watch out for fumes & ventilate well ...they are probably worse for you than sparking up a ciggy ! * Be careful with Ferric cloride pcb etcher, its highly corrosive, eats metal & also stains everything.. especially clothes and skin ! Follow safety notices & observe COSH handling & storage proceedures. Reccomended to be kept in the supplied container, or if you make up your own mix.. in a glass jar, stored in the dark ..and keep away from sunlight. when etchant is spent.. it'll have gone from orange to black ..to a final greenish colour apparently. (note: apparently through electrolysis it is possible to revive etchant by plating the etched copper onto a copper probe; dont try this if you dont know what you are doing !) * Ferric cloride works best if warmed up a little; about coffee cup temperature .but definately not boiling ! ..I heat up 1/2 litres worth up in a microwave for 2 mins ...tho i dont reccomend doing this. * Etch in a plastic tray (or glass jar), metal ones of any sort wont work ..and will be eaten by etchant. * Etching solution requires constant movement to do its work quickly; rock solution in tray ..or suchlike. * To cut pcbs without a decent gilotine; score them with a stanley knife, then place the board on a surface with the cut lined up with a square edge. Place a wodden block on top & hold down firmly; use pressure with other hand on exposed pce & snap off. * To see one of the american pages i read on this method; Click here: http://www.fullnet.com/~tomg/gooteepc.htm#1
-
yeah, i know all about things like the mining trades.. it is insane.. but people will do whatever it takes, if they stand a chance of getting stinking rich ...greedy shallow bstrds. ..tho there you go. Mercury, well talking of this obscenely dangerious heavy metal; and noting with irony how stringently regulated some areas are to avoid exposure to such substances... did you know that it is used in those shiny silver amalgam fillings at dentists & also as a preservative agent (thermosil ?) in a number of vaccines ...and someone saftey stamp approved it ! ...even if there was no -theoretical- risk ...i sure as hell want to stay well away from heavy metals regardless ...hmm better be careful processing pcbs then ;) :)
-
http://atari.digital-madman.com/ Oh.. heres something else in a similar vain ..tho mostly tieing into the dodgy dumping business & sordid business practices aspect.. Its an ongoing investigation by an Atari fanatic who wanted to know weather the stories of Atari dumping 12million ET carts & a total of 12 truckloads of other stuff in a new mexico dump & concreteing 'em over in the 80's where true... So far he seems to have confirmed that it actually happened. ..oh, it also has to be said that it is true that as you might expect at the beginning of the silicon computing era, big companys overcharged for their products & where certainly not keen on making cheaper revisions. This could be partly explained by the huge size of such companys, their need to keep paying for staff & facilitys & the huge past R&D bill to get the product onto the table in the first place. And whilst it is nessursary for companys to offer parts at prices that allow manifacturers to make and sell their items at a price the market will take an interest in & sustain ...whilst allowing enough room for a meager profit... There will always be loads of cowboys who take up the oppertunity & go about business anyway they can; with no regard for the impact & damage they leave in the process ..to steal the market and make a quick buck. Having said that.. This goes on allot ...even these days, at all levels of business; at a huge unsustainable cost to our enviroment. Tho to be honest of the situation, theres lots of dodgy people in these sorts of business.. Just that often the really shifty ones get attracted to the sort of oppertunitys that MOS took.
-
Ok, Pulling as there is a potential copyright issue on the reproduced content. Although its highly unlikely to be infringing in the ways that they might feel compelled to enforce it. I will remove the content & people will simply have to read the post on the site. Thanks for the extra insight, and yes.. articles written by people in a fashon which does not allow them to be contested; allows for unfair bias ...so at least in discussing that here, we can go half way to righting that.. Maybe if such a post does not exhist on wikipedia; maybe someone can start it ? :) Regards, Artesia.
-
http://www.vintagesynth.com/sci/birth.txt Found this interesting snippet of history on the web.. ever played with a WaveStation or the likes ? ...well this is where it all started :) _____________________________________________________________________ The Birth of the Prophet VS By Chris Meyer, ex-employee of Sequential Circuits reprinted from the VS WaveWrangler User Guide by permission of Interval Music Systems, ©1991 Interval Music Systems. It all started somewhere in 1985. We were still working on the Prophet 2000 sampler, and as resident historian (in other words, I had the most magazines and manuals) another engineer was asking me to explain how various instruments performed crossfades. I had finished discussing the Fairlight, and had moved on the PPG - explaining its wavetables, and the ability for it to scan a group of waves first in one direction and then back again, While I was scrawling this back and forth motion in my notebook, suddenly a little twinge went off in the back of my head, and myhand drew the next line arcing down the page.. and the concept of crossfading beween waves in two dimension, not just one, was born. Trying to imagine what it would sound like to wander around a space with different waves in each corner was a little beyond my grasp at the time. So, I decided to patch it up on my rag-tag modular synthesizer at home. For some reason, I was convinced that all four waveforms had to be at exactly the same frequency, with their only differences being their waveshape (and therefore, timbe). I plunged into my aleady heavily-modified Oberheim TVS 1-A (Two Voice Synthesizer - a pair of old SEM modulars, a sequencer, and a three octave keyboard in a road case) and found a way to sync all four oscillators. I then dialed up four different waveforms by playing with the waveshapes, sync tuning, and filters (since the TVS has only two filters, I used my hand-built linear-based PAiA modular for the other two, using a Korg exponenial-to-linear convertor to make sure they all tracked the Oberheim's keyboard together). I then patched the four resulting VCA's from a custom cabinet built by Gentle Electric, using the various control voltage mixers built into the Gentle Electric and the inverers and bias offsets in a Dennis Electronics Control Voltage Processors to perform the crossfades. The timbre mix was animated by envelopes from a Sequential Model 700 programmer and an LFO patched in from the Oberheim. This was all mixed together and fed into a final VCA, controlled from the Oberheim. In the end, one voice took up almost my entire collection of ananlog synths, spread across modules from six different manufacturers. It took about an hour to learn the patch (trying to mentally map a pair of ADSRs into i maginary two-dimensional space while my hands probed around a maze of wires...lets just say it took some thinking). Yet even on this limited system, some pretty intersting timbres started to emerge - struck attacks that faded into shimmering flutes; clarinets that opened up into raw sawtooths, etc. I took this tape into work and played it for a few engineers, and after getting some ribbing for my bad playing, they got excited. As interest started to build, I started lobbying the marketing department to consider this new idea. I played them a tape of The Fixx, (where the keyboardist plays a Prophet 5 and a PPG Wave), and told then that we could design one instrument that could make all of the sounds. (The whole issue of what the VS would end up sounding like finally reached a head when the director of marketing stated to demand - well into the project - "Can it make the sound of a DX7 slap bass? If it can't do a good slap bass, I want out of the project right now". We just laughed at himn and said "We don't know what it's going to sound like!!!". Thankfully the VS didn't let us down...) At this time no engineers were part of the product planning meetings at Sequential, but as luck would have it founder Dave Smith was talking about starting work on Sequential's first digital synth and trying to find a technology that would allow the waveshape to be changed in real-time. Just like people say, timing is everything. The team of primary engineers became myself, Josh Jeffe and Tony Dean (the latter two who now work at E-mu). Tony ended up being the main hardware engineer on the project and Josh the main software engineer and project manager. We spent alot of time trying to refine what I was calling "The Diamond Patch" (so-called for its brilliant, shimmering sounds.. and other more vain reasons I'll reveal later), and figuring out how to to design the hardware. Keep in mind that none of us had any background in DSP or psychoacoustics; we had to make it all up from scratch. As it turns out, some of our ignorance paid off in taking paths that textbooks would told us to avoid. Tony and I theorized on how to do a wavetable synth, and came up with two strategies - have a waveform of short, fixed length and vary how fast you played it, or start with a very long version of a waveform and skip samples in it to alter how long it took you to read it out once (and therfore alter your final pitch). Unable to decide we acquired a PPG anda Korg DW6000 to see how they did it. We felt vindicated to learn that the PPG did it exactly the first way we theorized, and the Korg the second. (In the process, Josh became one of the few people in the US who knew how a PPG worked inside - the company didn't release schematics, advising would-be techs to "Don't loose (sic) time - return to factory immediately!"). We liked the pure balls of the PPG better (plus the scheme that used shorter waveforms meant we could stuff more waves into the instrument), so we chose the transposition method. This choice is the one place our ignorance paid off the most. Transposing a waveform way down in pitch causes strange upper harmonics - images of the original harmonic pattern - to appear if not properly filtered. These images are what gives the PPG (and VS) its brightness and vicious bass. I was raving for months (much to the bafflement of Josh and Tony) in particular about the sound a PPG makes where only the low and highest harmonics seem to be present. One day, I walked into the lab while Josh was testing the VS hardware, and happily exclaimed "That's it! That's it!! That's the sound I mean! What's the waveform?" It turned out it was only a sine wave, but it was tuned so low that the image of its one harmonic was audible as a very high, airy harmonic. Working on a sampler at the same time really tuned our ears to the difference between natural sounds and synthesized ones. Most synths of the time went through some interesting gyrations with their envelopes, but then stopped any harmonic development when they hit their sustain stages. Also, real sounds have a lot of phasing and beating going on, which is too complex to recreate with just a simple LFO. The first major change to the Diamond Patch (a name that curses Vector Synthesis to this day... it would be much easier to use if the four oscillator positions were the corners of a square instead, but Josh felt the name demanded that the user interface arranged them like a diamond - which everyone has followed ever since) was to allow the four waves to be separately tunable. Detuning provides a type of motion and beating that no amount of timbre variation seems to be able to replace. Josh tried all sorts of algorithms to simulate detuning in oscillators that were actually synched together, but all had weird artifacts. In the end, it was best that they ended up the way they did. (Speaking of sync, we considered that, but Tony didn't feel he could guarantee that it would work reliably in the custom chips. Oh well...) Another step was to borrow the looping envelopes from the Buchla 400. I had spent a little time with that particular beast, and enjoyed the extra motion I could get from its independant, ten-stage, loopable envelopes. Each envelope became a sort of complex LFO, operating at a frequency that was different than all the other envelopes and LFOs. This came the closest to imitating the almost-random motion we were hearing in real sounds. Josh and I argued over the number of steps in the envelopes for some time - I wanted more steps than the normal ADSR, but he didn't want it to be too complex for the the musician to program. He finally came up with the idea of a five-point envelope, where point "0" could be used as an instant-on attack without wasting a whole stage with the envelope rate set to zero. Scott Peterson (my immediate boss, and one of the original Sequential employees) came up with the idea of the joystick to control the waveform mix. This proved to be a lot easier and more intuitive to program than the discrete X and Y axis envelopes I used in the origianl Diamond Patch. It also fit well with the idea to include user waves in RAM - the user could then easily dial up a mix with the joystick, and press a button, and have their own custom waveshape. We felt this feature would really make the VS a timeless instrument, since the user could keep renewing and personalizing the instrument as they went on. Alas, this has never really been expoited until the advent of the the Wave-O-Rama portion of the program you're holding now [VS WaveWrangler]. The original waves for the VS were created three ways - extracting single-cycles from sampled sounds, using a custom additive synthesis program, and using a program Josh slapped together called "Hacker" where you could draw the waveshape. These were fed straight from the computer through the filter and VCA of a Pro-One to figure out what the might sound like in a patch. And by the way, no PPG waveforms appear inside the VS - we had access to them, but in the end our consciences got the better of us. We did steal some waveforms from the Korg DW6000, but only by looking at the harmonic drawings on the front panel and trying to imitate them in our additive synthesis program. The VS is really quite a mess inside hardware-wise. We had problems with the custom chips being developed for this product, and we were trying to push the analog multiplexing circuitry further than it really wanted to go. (We considered trying ot so the waveform mixing digitally - dedicating a 68000 or TMS320 to each oscillator - it ended up cheaper to do it in analog.) But some of the nastiness is what gives the VS its character -this guy does not fadeinto the background in a mix. The very first patch I remember coming from the VS was created by Josh.It was pretty simple - four disparate waveforms in each corner, with one LFO panning between A and C and the other panning at a different rate between B and D. The resulting extreme washes between radical harmonics and simple sine waves ended up being an example of the signature sound of the Prophet VS. How did it end up being called the VS? Well, no one was really thrilled with the name "Diamond" or the term "Diamond Patch" (vain admission - I thought "The Square Patch" sounded too boring, so I rotated the positions of the four oscillators 45 degrees to look like a diamond - a decision I regret to this day, because it meant the four oscillators have stayed rotated 45 degrees in the VS and its descendants even though they make much more sense laid out as the corners of a square).Also we didn't want to give it just another number (its project code was 2400, and the "Prophet 2400" was indeed considered). Josh was sick one week with a bad cold, and was taking a lot of Sudafed Plus one day to try and get over it. Now, those who have taken it know that Sudafed is indeed a mild amphetamine. While in this drugged condition, Josh got the idea to call the process of defining the waveform mix "vector synthesis". We called Dave Smith in Hawaii (where he was preparing for another Iron Man tournament), and the incredibly sick Josh had surprising little difficulty convincing the incredibly fit Dave to go along with it. (The Random Patch feature came from another Dave/Josh exchange. In the lab, we had one prototype VS wake up brain dead. In the process, it scrambled its patch memory, and was producing some of the most bizzare sounds as a result. Dave - an aficianado of bizarness - therefore wanted a patch randomizer built in, but Josh was against it. Finally Dave promised Josh a six-pack of his favorite beer if he would put it in, and in one weekend Josh slapped it together. Ah, the scientific process...) What did we leave out? We briefly considered adding attack transients in front of the waves, but ruled it out for lack of RAM. (I, for one, was sick in my stomach when the Roland D-50 came out with sampled attacks). Sync, velocity to attack rate, and another stage in the envelope are onmy short list of other features. Its ironic that so many years later, Vector Synthesis is considered a Hot Thing - especially when you consider that neither Josh, Tony or myself sworked on the follow-ups from Yamaha or Korg (althogh to be fair, Scott, Dave, patchmaster John Bowen and tech writer/philosopher Stanley Junglieb did). But it's still the one instrument I would take with me to a desert island, and I'm proud to have been a part of it. Chris Meyer is now Chief Engineer at Roland R&D, Los Angeles, California
-
well.. although it might be possible to build something which has its general structure, i doubt its particular character could be obtained, it uses a bunch of custom chips engineered around the design of the old prophet's curtis filter chips ..amongst other things ;) Also i would love to see wave table synthsis cloned on a diy basis ..it would be so much fun to dabble on with. There is a user built project on the web.. who built his own wavetable synth.. however it was designed as a complete synth.. rather than just a voice module ...so it'd take some picking appart to remake it the way you wanted to. Yeah, its quite expensive.. then again its way less than the moog & has moe to show for its circuits ;) Sure has features in common with many other keyboards... however theres much about it thats different enough to well and truely avoid it being just another 'me too' product. it would however be pretty easy to clone a moog ...they are well understood electrically, and all of the components are available off the shelf ..for way less money (5-20%) than a brand spanking new voyager v3 ;) also, id love to see the person who makes a decent weighted, velocity sensitive keyboard from scratch ;) ...thats an awful lot of work making all those keys alone ..let alone the mechanics to mount em' up... Guess you could buy raw keyboard units, but thats cheating right ? ;)
-
Hi Stryd, Yes well, casualty of spontainious enthusiasm, i guess it could be seen that way... i just cut n pasted what was on the website, ill edit it down to the facts, if admin objects... they are welcome to delete the post... i dont mind :) All its about, is of all the new commercial synths i've seen float by lately (well analogish ones anyways...) ...this is the only one which really caught my interest as being pretty fun & well rounded ..allbeit its a bloody expensive beast for the somewhat pretty keyboard version; however its heap loads more value / sound diversity for your money than a moog voyager ...which is still very nice btw. and no, i have no connection to Dave Smith, wish i did tho... as i might get a discount ;)
-
you could try mixing with valves in the signal path... Then you could indeed play the danger high voltage ! game.. Dont ask me about large frame helium neon power supplies ....you really don't want to know ;)
-
...Wimper ..Drools uncontrollably, and fleeces his pockets for change ;) :) Excellent on everything except polyphony, and you'd probably not need that.. http://www.davesmithinstruments.com/polyevolver/design.html Some blarb & specs from the website, edited down.. if you are all that interested.. please see his site for more.. Poly Evolver: Specifications The Poly Evolver Keyboard has a 5 octave keyboard, 77 endless-turn knobs, and 59 switches. The keyboard is weighted 5 octaves, with velocity and mono aftertouch (pressure). It measures 38.5" wide, 14" deep, and 4" high, and weighs 23 pounds. The Poly Evolver Rack is a 1U 19" rack, and is fully programmable from the front panel. It also comes with a free Mac/PC editor. It measures 19" wide, 9" deep, and 1.75" high, and weighs 6 pounds. Operation Manual/MIDI Spec Specifications; Keyboard and Rack last Updated May 2005 4 Banks of 128 Programs for 512 total Programs; 3 banks of 128 Combos (384)- dump to/from MIDI The internal controllers and DSP chips can be reprogrammed via MIDI, for easy feature additions The following specs are for one of the four voices, so multiply everything times 4: .Four oscillators in total: two analog, two digital Analog Oscillator waveshape are Sawtooth, Triangle, Saw-Triangle, and Pulse (with voltage-controlled analog Pulse-Width modulation) Digital Oscillators select from 96 wavetables from the Prophet-VS (128 words x 12 bits), and 32 user-loadable (via MIDI) Wavetables (128 words x 16 bits). The Digital Oscillators get trashy as the frequency gets higher, as with the original VS. Hard Sync on the analog oscillators FM and Ring Mod on the digital oscillators Separate Glide per oscillator, with two glide modes Real voltage-controlled Curtis analog lowpass filters - not digital recreations. 4-pole/2-pole switchable, fully resonant (in 4-pole mode). There are two separate filters, one for the left channel and one for the right for a true stereo signal path. Analog Voltage Controlled Amplifiers (VCA), again one for each channel. Dual digital 4-pole Highpass filters (one per channel); place before or after analog electronics. Stereo audio inputs; Noise generator Envelope Follower and Peak Detect from External Input to use as modulation sources External Input can be used to gate envelopes and/or step the Sequencer Three fast ADSR envelopes Four LFOs (sync with sequencer and MIDI) Dual (left and right channel) tunable feedback loops; modulate frequency and amount Delay with 3 taps; each with separate time and amount modulation. Syncs to sequencer/MIDI. Normal feedback and additional feedback path through analog filters Distortion... Digital, one for each channel, can be placed before or after analog electronics 16 x 4 Analog-style sequencer - syncs with MIDI Extensive Modulation capabilities, including audio-range modulation. Bipolar (+/-) modulation.
-
Well, reluctantly the case size jumped up a whole unit size ..due to getting a 2u rack case at a radio show brand new for £3 ..rather than the usual £30 ish :)) Built Psu now, fully tested and ok, designed to supply 5v+ for the logic side, 12+, 12v- and +9v to account for the opl3 & the two different sid supply rails. Leds on top of each cap bank to show if theres a psu problem. All parts for psu recovered from free, scrap equipment :)) Transformers from old pcb modules of some sort, all regulators, diodes and caps from old Computer power supplies. Notibly the three capacitor banks are composed of about 30 x 6.3v 4,400uf caps arranged to make them suitable for the working voltages used, Got waaay too many of these lo-v ones & it seemed as good a place as any to dispose of them :) Overall the power supply is pretty overkill, at the end of the day, the regulators are the weakest link, and upgrading / adding to them is easy enough if needed. note: half of the sid boards loaded ...,4 more arriving shortly.
-
http://hem.bredband.net/bersyn/ Hi, check out this guy, he's been working on a quite an impressively well planned Analog modular using many classic part designs; he calls it the Bergfotron. There are clones / improved versions of many classic VCA's, VCO's, VCF's ..and the likes ...all with full schematics, some good documentation & pcb designs ! Warning... some of the designs are a taaaad complicated ! please check him out.. Hmm... now we need to get an affordable, buildable multichannel CV box, adapt these sorts of designs, drop the manual only controls (with respect) and make a full recall, automated Midibox Modular ;)
-
MOOG PRODIGY With AUDIO IN & nifty 'FM' feature FOR SALE...
Artesia replied to Artesia's topic in Fleamarket
now thats an analog modular: ;D http://www.cluboftheknobs.com -
MOOG PRODIGY With AUDIO IN & nifty 'FM' feature FOR SALE...
Artesia replied to Artesia's topic in Fleamarket
Its a mixed bag situ, i like the little box of tricks, it sounds nice :) Tho it hasnt got afew things, like midi (not that it couldnt be ucapps retrofitted ;), which means for the extent of its feature set it just doesnt get played with much here. So put it up on the market as theres many people who would love to own an original series moog... Whereas im happy to bide my time and buy one of the new one with memorys and midi when one hits the 2nd hand market, so i dont have to rely on my memory ;) Also i have to admit, one of the moog emulator softwares (which one i cant recall this sec) actually gets almost indiscernably close to the lush sound of a moog ..double blind test, id probably not actually be able to tell.. so that'll keep my moog fix in check for sometime to come yet... And i usually dispise analog emulations ...but this ones a goodie :) -
http://cgi.ebay.co.uk/ws/eBayISAPI.dll?ViewItem&item=150062027188 ITEM NO: 150062027188 Hi, Anybody fancy a moog prodigy, got one for sale.. listed up on ebay.. see the details above. Has some extra special non factory bonuses, an audio input for feeding stuff through the filter & also has a 'fm' feature added for brightening up those sounds & making some mighty weird effects :) Also, its one of the late models which includes the CV IN/OUT section as standard :)
-
yep, UC - Universal Control is cool.. A pretty clear discription of what it is :)
-
yes.. fair comment, i'd second that too.. tho it'll be upto illumantor
-
There's a gang of hamsters who take turns sitting on various bits (whilst trying not to get electrocuted (thats why the mains is boxed off); then they go sit somewhere cooler in the case to chill. thus transferring the heat & giving questionably more sense of purpose, adventure & comfort than a wheel & bottle feeder.. Been in London this past week recruting hamsters for the task, training & construction this week.. ..maybe i can get them off to an early start & they can help hold those troublesome bolts and screws in place whilst i fix them down.