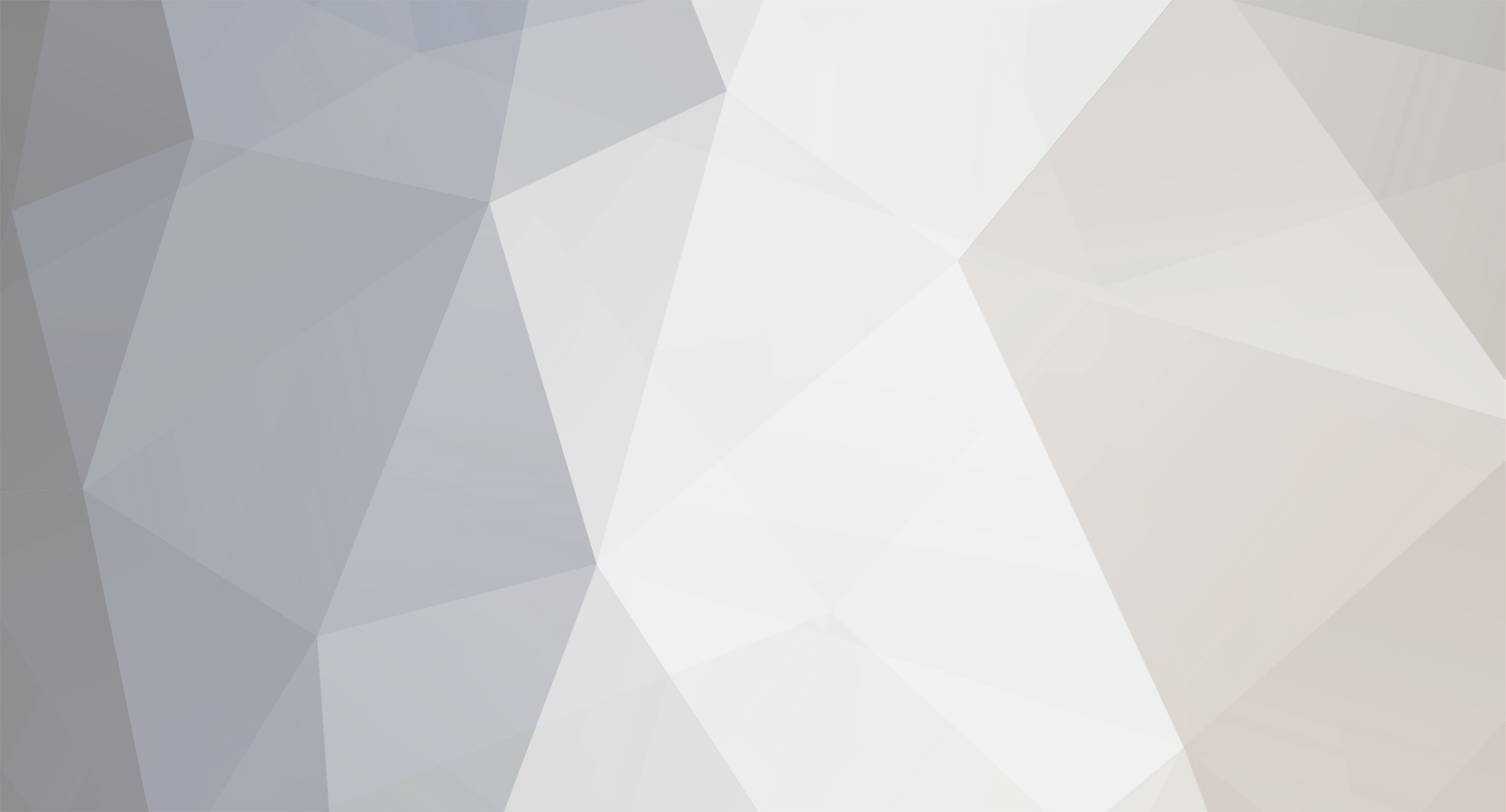
Zam
Members-
Posts
625 -
Joined
-
Last visited
-
Days Won
26
Content Type
Profiles
Forums
Blogs
Gallery
Everything posted by Zam
-
Hi Fantom I reduce at 10x now, I have debug message "time out" showing sometime at 20x, don't notice problem with it (maybe some intermediate data in a fast pitchbend change?), but it don't feel slower at 10x so for moment it's my daily use setup. Best Zam
-
Hey Chris Did you try bank ? EVENT_KB .....chn=1......bank=1 EVENT_KB .....chn=2......bank=2 EVENT_BUTTON...meta=setbank...toggle...range=1:2 Best Zam
-
Hi Skunks I suspect your analogue pot have some move at the shaft, or inaccuracy at the track ends. Try to set some dead band at AINSER (cf .ngc manual, pinrange= ). Best Zam
- 2 replies
-
- cc
- controller change
-
(and 1 more)
Tagged with:
-
Hi ! Best Zam
-
Hey That's great ! definitely waiting the feedback on this. Can you pleas send me the full data sheet if you have it ? Best Zam
-
Hi Gato Welcome here :) Ho ! I just check, you'r right they discontinued the dual track MF914 ! I don't know the MF9101 it's a new product, datasheet only offer math log taper (as the curve say). Maybe they offer audio log on request ? Looking at pictures tells me the track, material/dimension/pinout is exactly the same as MF914, change seems at mechanical side only. Have a look at LMH5 series, there is audio log or math log as standard options. You will see the difference between the two taper curve. Yes that's right ! (I just update the first post) I'm currently working at optimisation of .NGC/.NGR configuration, for mutli core (16 or more fader) handling in a Master/Slave setup. Like Solo an Mute status between system, as optional button functions at slave core but seen by DAW as main MCU unit (not XT). For the moment I run 16 fader with only one connection to computer (USB), computer see two MCU unit. Best Zam
-
-
Hello Benoit Thanks for reply. Not sure I understand everything right now, but if it allow to have at least 4 independent session (not merged like now) it will be great I know the analogy is not correct, but for my use case it should be like the USB cable which allow 4 midi port definition (16ch each ones). I need to send/receive 32 pitch bend, 8 per ports chan 1 to 8. If I'm the only one that need this it's little annoying to ask for it... Best Zam
-
Hi all I open a new topic at MIDIbox user project section for the release and support http://midibox.org/forums/topic/20390-midibox-89motion-fader-automation/ Best Zam
-
Hi all This is the MIOS based 89MotioN system release and support tread The first PCB batch is now available. It consist of 17 pcb to build a 8 fader pack automated motor fader system as follow: -1x 89InouT, 4 layer 80*260mm pcb, which handle 64 D i/o and 8 A i/o, connection to 8 89MotoR board, connection to core(or line receiver), and optional D i/o chain connector, and power supply distribution. -8x 89MotoR, 2 layer 34*116mm pcb, which handle analog PID motor driver, touch detection, one optional isolated digital output (optocoupler), one optional digital input (button), 6 D i/o through connector from 89InouT to 89 RemotE -8x 89RemotE, 2 layer 14*148mm pcb, which support up to 6 omron B3W-9 series illuminated tact switch. -all pcb HASL lead free Price is (out of stock) (+shipping/packing, +fees if applicable). 12 pcb set available from this first manufacturing what you get: -the 17 PCB described above -BOM -schematic -PCB mechanical drawing -Basic notes for build and calibration What you need for basic build: -all component at the BOM (most ref already fitted for RS and reichelt) 300/400euros -one STM32F4 core running latest MB_NG, configured to emulate Mackie Control. There is universal MCU template available, as my NG/NR config for DigitalPerformer i’ll be happy to share. (request 1 core for each 8 fader pack) -decent PSU, 3 rail total, +5V, +/-15(+/-12 work too). at least 2A per rail, be careful most low cost bipolar supply have poor negative amperage capabilities, sense input is recommended for the +5 rail (I use industrial euro rack Vero trivolt PK120, 500€) -8 motor fader (tested ALPS RSA0N 8V and TKD MF914 10V my current choices) 15 to 100€/pce -A console, a box or a front panel that fit the system (I can provide basic template .fpd file for fader and button cutout) 0€ if it’s a retrofit installation that need no metalwork to 1000€+ in a custom modular setup like mine… -For integration in analog chain you need a +10dB post fader buffer (for unity gain @ fader -10dB attenuation position), to my knowledge all descent console have it so you are fine, in situation of outboard analog mixing/summing you have to think about it. -line transmiter/receiver in case you need/want the core, PSU, SCS and or LCD in a separate/dedicated case or 19inch rack Important notes: This is a 2+ years R&D at hardware side for me, not to mention what TK have done since lot of years, as improvement and new options recently done at NG code which this system won’t work so well without. The goal since beginning is to build a high end automated fader system, dedicated to analog chain/mixing desk requiring low noise and low EMI environment, which is a challenge with digital data lines and motor close to low level analog audio signal. Saying all this I consider this build an « advanced » one, it involves 20 SMD ic at the main I/O board, I won’t do a step by step build tread, so ppl have to know how to read a schematic/BOM and understand what’s going on with all those component. It’s a long built we are close to 1000 component to solder in total… mistake can be exponential with so many part, no special skill, but methods and organization at all stages. My expectations for this first run is to have few fader pack builded around, in a reasonable time range, to have useful feedback and various experience to share. Also, it’s not a cheep build, consider 2-3k depending of hardware integration, motor fader choices, frontpanel + optional 19in or case if you want/need psu and core far from faders (like me, it request optional line driver) I have great result in my use case, 8 fader(for now) loaded in a discret 32 channel Studer 289 from 1977, however, I can’t guaranty the same result (in term of audio integrity) in another desk, if trouble occurs with digital data line or motor radiation, it could be dependent of specific console design/layout at both mechanical and electronic side. So I can’t say « I will solve your problem » but of course I will try to help. For ppl that just want a DAW controller (no analog audio path in the fader) there is possible cost saving, cheaper fader (like ALPS RSA0N11), lowering fader speed and increase current limiter at motor to use cheaper PSU. For ppl that want motor fader to automated a VCA based system, there is different option to handle this with the system, let’s have a talk if you are interested WARNING ! there is some limitation: -at the moment the system don’t support HUI protocol for fader data, It won’t work as is in Protools !!! Be sure your DAW allow MCU protocol, or have a look at some midi translator software, I made a quick test, and was able to convert pitch bend fader data to HUI raw midi data on the fly, I don’t and won’t push further at this topic for the moment, so I have no measurement or data to share regarding hypothetic extra latency. -Work in progress regarding HUI protocol, now the system handle it natively for all data type, I have a working midibox_ng 1.036 build, it involve a special handling of NRPN data at mbng_event.c (standard NRPN won't work but none are involved in HUI), as some trick at .NGC configuration file. I don't have a Protools licence but will perform test soon with someone that have one. -Another point is about MCU protocole, be aware that some functions are not bidirectional, and some are not « real time » bidirectional. Automation mode don’t return note or CC but only sysex text to print the mode at LCD, it’s still a challenge for now to update automation status LED from DAW All data except fader pitch bend are updates/returned to the system only once per sec, which mean the visual feedback (LED) is not ultra fast. Also as audio is picked-up pre fader at DAW, solo and mute can be complicated to handle depending of your DAW, here those functions are 100% handled onboard with optocoupled remote analog mute and special mute/solo conditional script. Mute automation is done via a separated midi track What I won’t do: -publicly release the schematic, at least for this firs run, and certainly for the few next. -release the layout/ pcb fabrication files. -organize any component and part bulk order /group buy for this first batch. What I hope to do next: -Be able to test TKD LMH5 series (I’m sure it will work fine with the driver, it’s the same 8V mabushi motor as ALPS), it’s an alternative quality between the MF914 and the ALPS RSA0N, which have an interesting mechanical build, to say it quick, motor driver PCB should be directly soldered to the fader terminal, vertical mount, which can be a nice option for future and mechanical integration option. So if someone plane to use those, just drop me a message to discuss about one or two spare fader for test at my side. -Test (me or someone else) a fader with coreless motor -Design a 89TransporT unit for the system, which should be a D i/o extension with button and led, maybe one rotary encoder, to have extended function and DAW transport interface in the same design. -Build a vst/AU plug-in if I can… or if someone have the skill and motivation for this, to have direct connection with the fader, without third party MCU driver. -Go further with RTPmidi, high speed, which combined with plugin should allow the system to have way more than 32 fader in a single channel. -all other things that will com up in mind by the time… Quick technical data: -2000 steps, which equal to 0.05mm for 100mm fader. Theoretically 2048 (11bit), but some dead band are involved depending of calibration and fader curve mapping -100ms for full travel -Repositioning accuracy better than 0.01dB (at static event) -fader tracking is 0.1dB for 2/3 of the fader (upper side) if dedicated interpolation map is used for each fader (it’s some time to measure and write in the config file…) otherwise one global interpolation map for all fader give you at worst the fader attenuation accuracy given by the manufacturer. In short, the system is more precise than any manufacturer taper print you will find. I hope future builder will have fun with this great tool, which to my knowledge is the first analog fader automation available for DIYer If interested just PM me Best Zam the development thread http://midibox.org/forums/topic/19166-fader-automation/
-
Hi Jerome Thanks! Just to clarify one point, the sequencer video is a not a "special" mode (of course it could be implemented with another NGC/NGR midi configuration) It's a short multitrack audio loop, whit automation play/rec on the fly Voilà Zam
-
You should try my two non regulated tube microphone psu 'night Zam
-
I don't see any reason a SMPS won't do the job. Best Zam
-
Hello jaytee Is there a local regulator at the MB6582 for the 5V rail ? because the supply you show is 12V In this case we also have to know the amperage at 12V supply output, not only the 5V rail... For the 5v rail, If I do little math, 4 SID installed is about 90mA per SID, considering all other component and the 70mA/SID (datasheet I just read) I gess it make sense (I don't know this build) Now adding two SID increase to 550mA, which is 200mA more, 100mA per SID, for two SID alone (all other component idle already in the previous measurement) So your already have a problem at this point, not enough to shut down the unit, but supply start failing... Try another PSU, (and use an autotransformer if you can for this kind of trouble shoot) Best Zam
-
Hi As you only talk about add/remove IC and not swapping IC, maybe one of the IC dead and shorting Vcc Vdd? Best Zam
-
Hello jaytee Maybe the first to do is to measure the actual current at your build. As the voltage drop resulting in the inability to power on the unit. What you describe don't automatically come from a underrated PSU... Best Zam
-
so... my idea was not good. no more ideas for now at my side :/ Best Zam
-
What about this ? MAP1/BYTEI 0:0 ^val:64 127:127
-
Hi Chris I doubt you can put a syntax like this in MAP definition Not sure about but deserve a try: You can put ^val in MAP definition IIRC So try to define ^val with your EVENT_AINSER Another possible way ? predefine few MAP for your velocity and, use a toggle button to switch between MAP ? Best Zam
-
Hi My box don't require (for now) lit LED at startup so I don't go further. I see two option right now: -NGR with : set/change led at section 0 -a snapshot Best Zam
-
Hi You have to set initial value for LEDs too ? EVENT_LED id=17 value=127 EVENT_LED id=18 value=0 EVENT_LED id=19 value=0 EVENT_LED id=20 value=0 EVENT_LED id=21 value=0 Also IIRC I have same kind of issue you describe here, try to put led event definition before or after (don't remember) the other button/sender definition. Best Zam
-
Hello ilmenator Your welcome ! You already fix my mistake and missing sytax. One last point, I don't know if you need to also control this from external. In case, it will work with an event receiver fwd to sender 1 as I previously say, but you will have a loop with your sender 100 (hw1), I think you can remove this event and just use directly the button to send CC. Also you need a mechanism to update button value from external CC otherwise you will have offset and jump at toggle function something like this: event_receiver id=1 fwd_id=sender:1000 type=CC CC=103 range=MAP1 ports=10000100000000000000 event_sender hw_id=1000 id=1000 fwd_id=sender:1 event_sender hw_id=1000 id=1001 fwd_id=button:25:2 if_equal=2 event_sender hw_id=1000 id=1002 fwd_id=button:25:26 if_equal=26 event_sender hw_id=1000 id=1003 fwd_id=button:25:52 if_equal=52 event_sender hw_id=1000 id=1004 fwd_id=button:25:76 if_equal=76 event_sender hw_id=1000 id=1005 fwd_id=button:25:102 if_equal=102 event_sender hw_id=1000 id=1006 fwd_id=button:25:125 if_equal=125 Best Zam
-
Hi all Here is a new one, mostly playing with grouping and various waves/random automation (play mode) No audio involved here Best Zam
-
I just have another idea without NGR but radio_group for led not sure it will work but it deserve a try at NGC MAP1 2 20 38 ....120 EVENT_BUTTON hw_id=(direction) fwd_id=sender:1 range=MAP1 button_mode=toggle EVENT_SENDER hw_id=1 id=100 type=CC CC=xx #to send out the CC EVENT_SENDER hw_id=1 id=101 fwd_id=led:(up):127 if_equal=2 radio_group=1 #UP EVENT_SENDER hw_id=1 id=102 fwd_id=led:(down):127 if_equal=20 radio_group=1 #DOWN EVENT_SENDER hw_id=1 id=103 fwd_id=sender:2:127 if_equal=38 radio_group=1 #UP&DOWN EVENT_SENDER hw_id=2 id=201 fwd_id=led:(up) EVENT_SENDER hw_id=2 id=202 fwd_id=led:(down) EVENT_SENDER hw_id=1 id=104 fwd_id=led:(random):127 if_equal=64 radio_group=1 #RANDOM etc.... If it work, it's also an easy way to lit led from incoming CC with EVENT_RECEIVER .........fwd_id=sender:1 Best Zam