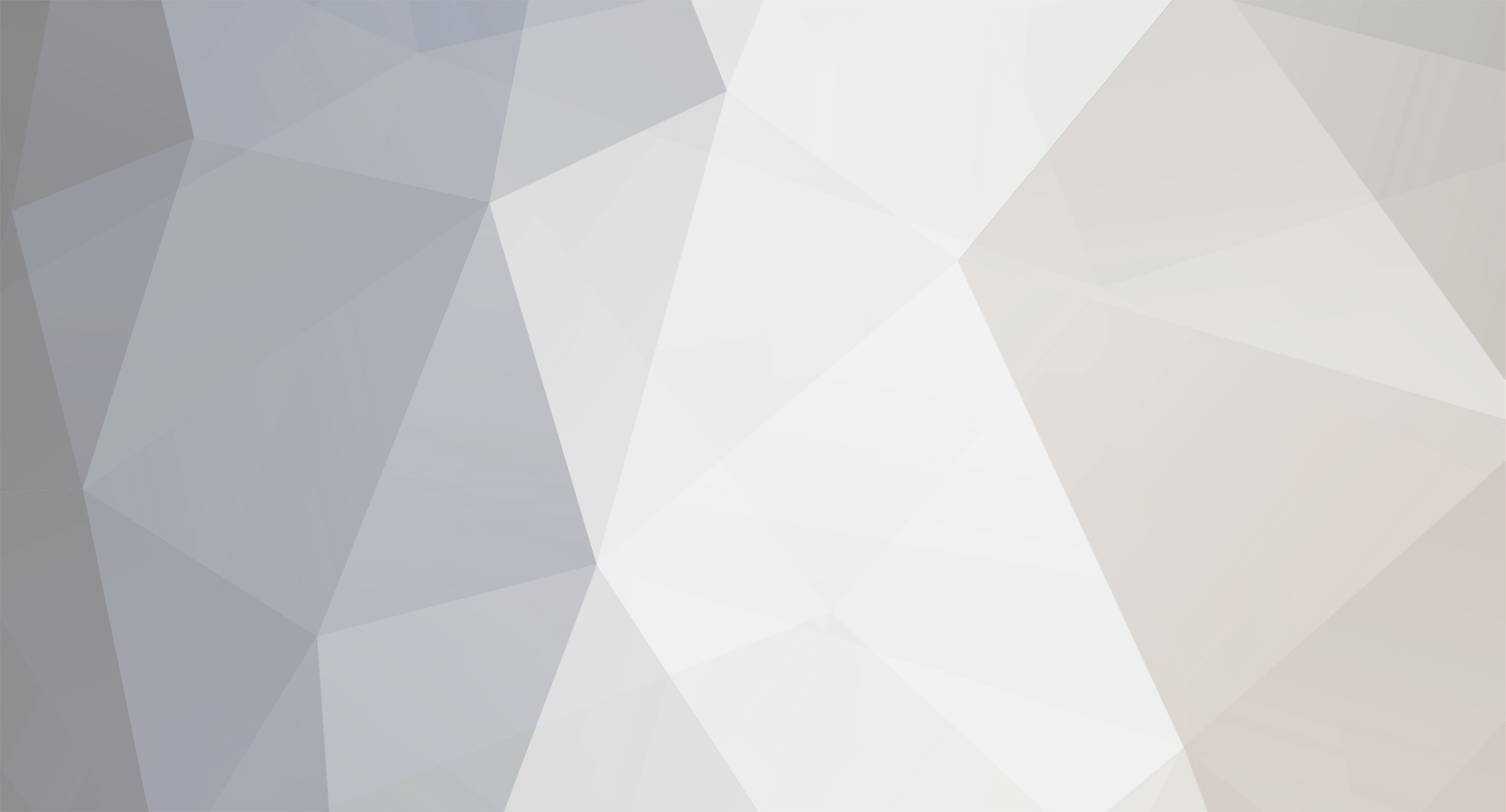
MRE
Members-
Posts
191 -
Joined
-
Last visited
Never
Content Type
Profiles
Forums
Blogs
Gallery
Everything posted by MRE
-
Your 'Rock out' rating is determined entirely by the intensity in which you mash keys. Velocity sensitive. PSHAW! the AUDIENCE is velocity sensitive yo! Gotta smack dat phone to to boost the street cred.
-
With the power of Oxyclean, for those tough dried in wine stains!
-
have you considered a switching regulator for the 5 volt supply? higher part count, a bit more expensive, and a little more board space, but in the long run, MUCH more efficient.
-
good luck to you
-
ahh right right right! yes. Funny thing is I had 2 mm cord in my head to begin with.
-
I would advise leaving the caps alone for the moment. Regardless of their values, they are unlikely to be the culprit for the overall problem. Once THAT is solved, you can always fine tune your caps. The O-scope will be a big help doing that. While it is true you would want to increase the 'storage tank' capacitor (the larger value one) when you change from full wave to half wave, you generally can leave the smaller cap alone. (In fact, you might find it works just fine at the first value you came up with) The larger cap is there to serve as sort of a battery. It charges up and maintains a high enough voltage to keep the regulator going during the downswing of the transformer. The smaller cap, is more of an filter for transient frequencies. These can happen anywhere, but often during zero crossing (imagine having home lighting kits bursting data during that time for instance). By the way, via spec sheet of the 78xx regulators, immediately before the regulator, you should have a .33uF cap. It is only REQUIRED if there is some distance between the reg and the PSU filter, but still, a good idea. Likewise, immediately after, you should have a low value cap no lower than .1uF. Anything lower can clunk it out. These additions *may* help with your ac hum. Anyway, to the gremlin at hand: I'm not sure, but I think you have a quarter wave here. I've never designed a psu this way, so I don't know exactly what it will do. I might dig out Electronics workbench and make a sim of it just to see what it looks like. I would suggest the following steps: 1 - throw that diode in transformer --[>|---(caps)---regulator Do this first, as you may be damaging that reg as you use it. 2 - check with an o-scope both before the diode, and at the regulator. nununu - pretend that is a normal 60hz sine wave at whatever output voltage your transformer provides (both outer terminals). nnnnnn - full wave rectification (after the bridge on the top side circuit, referenced to ground, REST OF FILTER/REG CCT DISCONNECTED) n_n_n_ - half wave rectification (lower end after diode. rest of circuit disconnected. If you get this, you can still use it with a large cap) You can actually test for this easily. Just use some clip leads to attach one end to the transformer lead, and the other to the diode. Now clip the scope to the opposite end of the diode. No need to connect to the circuit. Use the ground reference built from the top side. n__n__ - quarter wave rectification (lower end after diode. rest of circuit disconnected. If you have a long period after the wave, or it is considerably smaller peak than you expected, you will need to redesign your psu. It will be quite difficult for a cap to keep the regulator stable) WITH the filter and regulator circuits connected (i.e. oscope probe at the regulator), you will get a different wave form... It is hard to do in ascii art, so I will try to describe them: Imagine if you cut just the very tops of a sine wave. Now as you come over the top and crest the wave, rather than falling down the other side, draw a diagonal to the next peek, just below the top, and start again. looks kinda like a rounded sawtooth waveform, but the right side is stretched way out. That effect is caused by the discharging cap. That is the ideal waveform going into the regulator. If you get a peak, with a long fall-off that eventually hits zero.. you have a problem. If it stays at zero any length of time before the next wave comes, you have an even bigger problem.
-
How did you arrive at these numbers? What equations did you use?
-
I will have to think over the other questions.. but as to the question about just using the outer taps: That is the "typical" design. Center taps are great if you need a negative voltage supply. Other than that, most (if not all) designs I have seen were either multi-coil (custom and expensive) or simply took the outer taps and applied them to both regulators. You are right, it is not efficient for the 5 volt supply, and you will need a hefty heat sink. Another (bulky) option would be two transformers, matched to the desired output. I can re-post all that info about transformer selection if you'd like. I'm not saying your design is not viable... just unusual (and certainly creative). I will dig up the calculations for those caps. I am afraid though that I would only have calcs for full wave and half wave. In your case, the only way to know for sure that you have the right ones might be some experimentation (as any suggestions I could give would be based on doubling the half-wave calculation and the regulator data sheets). Do you have an o-scope? Not some home built ADC/PIC etc kit that is only good for 5 volts. I'm talking about something that you can look at those transformer outputs with.
-
Umm.. not sure I get you here. Steeping up the voltage will allow you to get away with thin cable, only if you plan on stepping it back down to be used. at what voltage is your load operating at, compared to what voltage you would be stepping up to? In other words: If you are planning to use the inverter to drive the lamp voltage up to 220, then you still have the associated thick cables required to operate whatever lamps you are intending to use, SAFELY. Are you planning on stepping up to 220, going somewhere with it, then stepping down to 12 to drive the lamps? Then you will have an ARSE load of transformers all over the place. Saving on thick cable and replacing it with heavy transformers, for 5 feet of gain.. doesn't sound very cost effective. Neither is going to save you on over-all current drain either. If you are short on money, then its a sure bet that an inverter capable of handling that much wattage is going to be a strain on the budget anyway. Add to it step down transformers (where needed), and you have a very convoluted system. So, Practically, I think your best solution might be: Large battery (car, or marine) --> thick cable --> distribution box (triacs) --> thinner cable --> 1 12volt lamp (or string of small series/parallel lamps). Figure that a 50 watt load at 12 volts still needs about the same size lamp cord as a 50 watt load at 120 volts AC. An automotive headlight would be slightly thicker. If you stick with Automotive lamps (Headlights, tail lights, interior lights, etc) you cant go wrong. The cabling requirements are pretty obvious, and if not, you can always ask the shop clerk. If you are using much more than the 4 head lamps, I would use two car batteries in parallel. In case this isn't already obvious: A large lamp, regardless of its voltage/current format, will require a large cable. There is no way around this. A load is a load is a load. Trying to shortcut this is asking for fire. 2500 watts of lighting is going to take some current, and is going to create some heat. No way around it. Perhaps you should reconsider your plan. If LED lighting is too expensive (think of the safety of the poor girl), then perhaps it shouldn't be done.
-
PS- That diode would be going between the transformer and C2. Quite honestly, I think even if it is NOT the problem, it would still be prudent to have one there.
-
Sorry my contribution is nothing: but I laugh every time I see the thread subject. It makes me think of things that would get me fired. "Hey! Nice KNOBS!"
-
Might have been covered already (I admit I didn't read ALL the posts in the thread)... Have you checked the input to the lower voltage regulator (I think this is your 5 volts)? Are you certain it is not AC there? I *think* you still need one diode here, because you are getting a push-pull effect on the input of the 7805. Yes, the top half still provides the ground reference for the lower half. That may, in effect, be the problem? In the lower half of the center tap, current flowing 'downward' would supply the VR, in reference to the bridge's ground. But when current is flowing 'upward' isn't it pulling current to supply the centertap to bridge connection? Also, if the bridge is supplying DC to the top half on both directions, and the lower half is supplying it only on half the cycle (one direction) then it is reasonable to assume that you will have less overall current available on the lower half. I DID notice the difference in caps, but I think they would have to be considerably larger to hold that 5 volt regulator stable (remember that *IF* I am correct, you are only supplying it with +current for 1/4th a cycle, and robbing it of current for 3/4ths). EDITThis would imply that even with a diode to fix the problem, you are still supplying it only half the available cycle, which would mean your caps would have to work awfully hard to supply a core, an LDC, and several IO boards. Your 5 volt supply absolutely needs to be full-wave rectified. If anything, it should be on the top end of the circuit.end edit So, is it possible that the caps on the right side of your 5 volt regulator are simply holding the slack for that LED every cycle, while the regulator is in fact dropping out most of the time? That would explain an overall apparent voltage of less than 5 volts, and the regulator would *appear* to be on. It pops in just long enough to charge the cap bank. They discharge over the period of the cycle (likely down to about 2 volts in reality due to the LED. Right about the time they give out, the regulator jumps back in to save the day. All of this on a DMM will look like the average of the upper and lower voltage limits during the cycle (whatever the REAL values may be). You really need to scope the input and output of the V-reg to know for sure what is happening. I dunno. That's just the impression I got from looking at the schematic. Something is fishy.
-
well dang.. I was too fast on the delete button then. Well, glad you got something out of it, and an idea for troubleshooting your current situ.. Ive looked over it, and Im a bit stumped. still trying to figure out the configuration to be honest. It is .. um.. unconventional. At least, its not a standard 'taught' design ;)
-
sweet project!!! :D I agree that the STM32 is the way to go here.... Lots of ram and processing power for more than one universe, and some pretty complex crossfade/step calculations for some really neat effects. not to mention more intuitive on the user side (graphic lcd? Possibly vga out?). lots of possibilities.
-
Using MIOS to control Christmas/Holiday Lights via MIDI?
MRE replied to m00dawg's topic in Design Concepts
Id stick with the midi to DMX512... Its been around for ages, its open, its robust, and it is the standard in the lighting industry (not counting the newer ethernet systems). If you start working with other protocols, you might get 'locked into' certain hardware and software constraints. DMX itself has had a hard time gaining traction with their new protocol (DMX2000 or some such) simply because there is already SO MUCH hardware that runs DMX. Why update if we don't have too? Stick with it and you can run intelligent lights as well. It would open the door for several THOUSAND pieces of old and new hardware. Don't waste your time reverse engineering a proprietary protocol. I would also suggest that since the MIOS32 opens the door for several com channels, that you implement a DMX input as well.. This gives you the option of DMX merging your signal onto the back of traditional light board signal. This gives you the choice of "whenever light x goes to %100, trigger midibox sequenced light event y." It would make it a VERY useful device for theater production, live events/concerts, and nightclubs. just my thoughts.... not %100 percent reliable ;) -
Using MIOS to control Christmas/Holiday Lights via MIDI?
MRE replied to m00dawg's topic in Design Concepts
In your quest, you should also check into DMX and Dimmer packs. Briefly: DMX allows for the access of 512 channels per 'universe.' Each channel can be faded from 0 to 255. The hardware is essentially RS485. You might elect to build a protocol converter using MB/MIOS. MIDI in, DMX out -> DMX dimmer/relay packs. There are several PIC projects for straight PC (RS232) to DMX control. They usually run into some limitations due to framing of the DMX packet. You might have some of the same difficulties. However, if I remember right, most of those projects were F84 based, and thus suffered from speed limitations, as well as having to bit bang two serial ports (DMX is a serial protocol, but very regimented). An 877 running at 20Mhz must surely be able to cope, with a lot of headroom to spare. -
It should be added that regardless of which project you choose, you will need to add significant signal conditioning and ranging circuits if you want to work with anything outside of 'digital' (0 to 5 volt) ranges. The front end signal conditioner from the first project is a good start. With some mods it could be attached to the FPGA4Fun design. Id still want to add a range circuit in front of that, before connecting to the probe, in order to protect all the expensive electronic circuitry.
-
Another short answer for you: As Ilmenator pointed out, MIDI is a digital standard. You do not need to worry about impedance here. You WILL, however, need to consider impedance on any AUDIO output/input circuitry, such as when you match AUDIO SIGNALS together, or attach them to speakers/headphones. MBSID is one example of where impedance becomes important. Thankfully, its all there in the circuit diagrams for you. No need to worry. 8)
-
Look over the FPGA4FUN project again. It is essentially pre-built for one thing. (Two built modules connected together.. 5 minutes to make this thing, another 5 to download the fpga software to the board). For another, and this is the most important part: 100MHz vs 1MHz. To be honest, that 100Mhz might actually be 50 if you want any accuracy. Nyquest says you need at least 2 or 3 samples to per cycle before you can trust it. So I would take anything over 33Mhz with a grain of salt. That is still WAY better than 1Mhz. To spend more than $20 dollars on something in the 1-5 Mhz range is silly. (Hand-held semi pro 5Mhz+ scope-on-the-go gear is excluded ;) If I were choosing between the two, Id spend the bucks, forgo the time and (marginal) troubles of building the kit, and enjoy the higher freqs of the FPGA4Fun project. It also looks like a two channel version is possible with a bit more work (and some cash). As well as the option for LCD output. Finally, function generators are not that hard to get, or build when you really need one on the cheap. I would assume everyone here would back me up on this: When it comes to o-scopes... speed speed speed. My handheld 5mhz unit isn't bad. 5Mhz is good enough for most basic bench work. Its portable and not tied to a laptop. And it runs on batteries for hours. The problem with it is that, while it can sample up to 5Mhz, the screen refresh is more like 1Hz. That makes it impossible to use on all but the most stable and repetitive signals. FPGAs are MUCH faster than a PIC for something like this. They were designed to be the digital signal taskmasters for the analog world. FPGAs eat, drink and break signal processing. Go with it, forget the PIC. (although, if you really need that function gen, there are HUNDREDS of cheap projects for 1MHZ and lower signal generators for PIC.)
-
Its a two stepper: 1) you must have declared the value when you shiped it, else you can only get the fixed min (100USD with UPS. dont know FedEX's.) 2) Prove the value. An itemized parts list with price quotes from multiple dealers helps, as does direct links to the website pn. The investigator must prove every price, so giving them links makes them VERY happy and fast. Next is your time...HARD to prove. It would help to show the build progress documentation from the forum! Important to note that you can insure for any random value but you only get what you can prove. Better to state an absurdly high price than to low. If you under valued it (or didnt insure at all and took the default) then you wont get more than that.
-
thanks! Wow, a person can find odd stuff around here sometimes. Im teaching EngRish in Japan, and this sort of problem with the language is particulary tough for people to wrap their heads around. Japanese is SO easy by comparison (not that my Nihongo is any good yet...)
-
got the reminder message too.. life gets in the way of constant forum drooling. ------------------------------- Please note that MRE not way a clone of MTE. The views of MRE do not necessarily reflect the views of MTE. However, we share the same policy on colorfull pill consumption.
-
What a great topic to come back to! Deffinately the current that kills. Everyone has been hit by 1000 plus volts every time you get shocked by that Office Space doorknob... but microampers (if not smaller). if you ever get tired of licking 9 volt batteries, try a phone cord.. thats a stinger. My all time favorite story thus far involves that electronic shocking game. I was challenged by the owner of one to a game. He claimed quick reflexes. Im certain mine are slow. After several games of two handed playing, he was complaining that "theres something wrong! I know Im winning, but youre not getting shocked!" "Well, I dont feel anything.. here, lets switch handles and play again..." buzz.. buzz.. "Fuck, yeah your paddles worked... OK, DONT try to win, and tell me if you get shocked.." "sure. ok.." Buzzz "urr... nothin..." "WTF?!!?!?!" After several rounds of this, (and me laughing my ass off the whole time) I finally reveiled to him that I was being shocked the whole time..and in fact intentionally loosing just to piss him off. Ive been shocked so many interesting ways that I can 'ignore' piddly games. Ohhh, damn.. and another good one.. similar style.. We were doing the classic neon lamp light by ... wait for it.. capacitor/inductor tank circuit. I got it all set up except for the neon lamp. We were supposed to measure the output first. I intentionally set the scope wrong so that it looked like a dead circuit. "dude.. Its not working.. " Im holding probes on the wires, with my fingers. getting buzzed the whole time.... "ok, you hold these here, just like I am.. and I'll probe the other parts of the circuit.. maby something will come to me..." "ok... AGH!!!" "ok, so remember that! Big pain can come in a small package. Never trust electricity." He continued to be my lab partner, and got 'smart' quick.
-
Hot glue face plates? Rubber Baby Midi Buttons?
-
ohh sure... cheese goblin... I see your point.