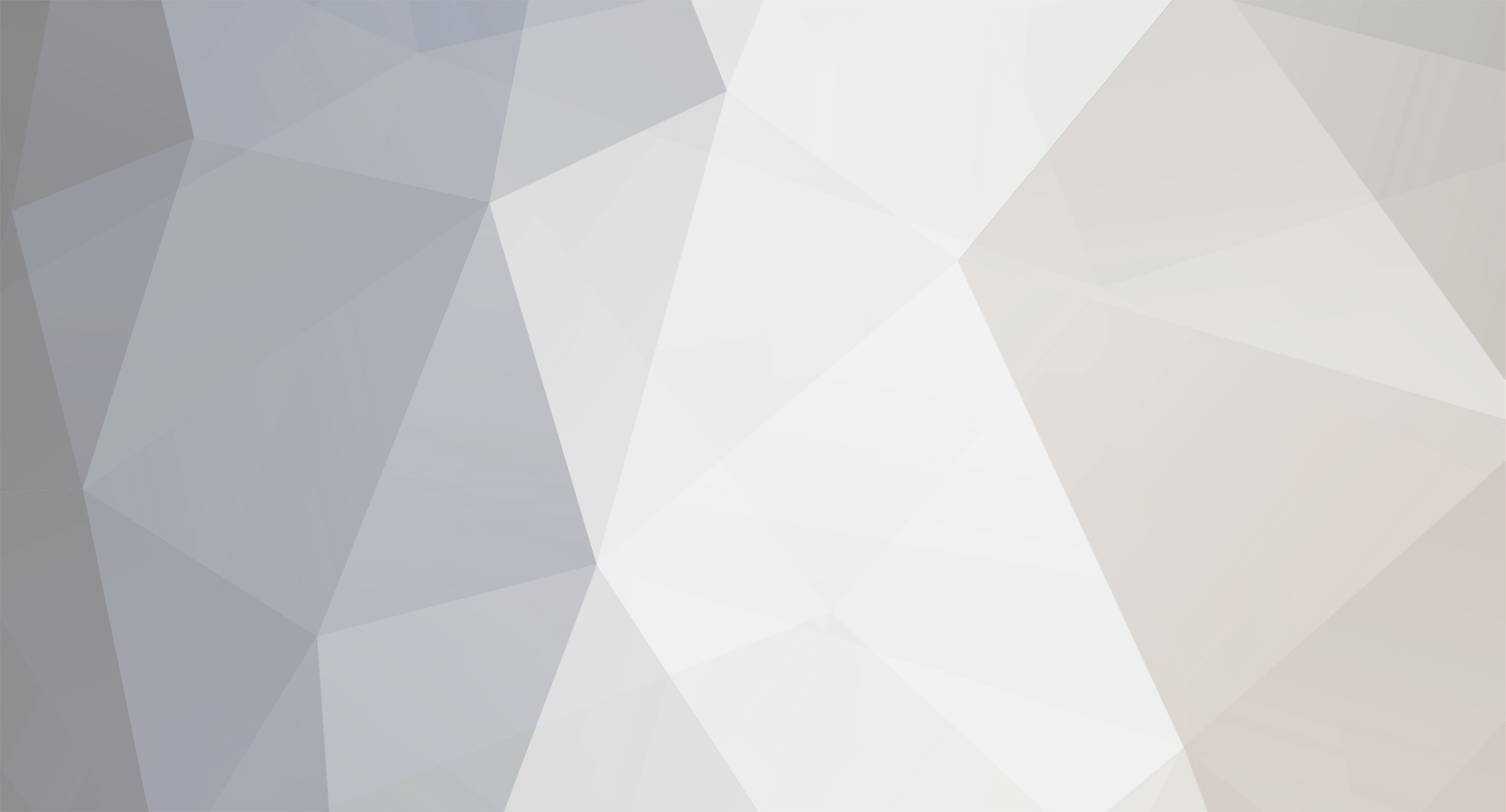
Arkay
Members-
Posts
81 -
Joined
-
Last visited
-
Days Won
6
Content Type
Profiles
Forums
Blogs
Gallery
Everything posted by Arkay
-
You're laughing then. The encoders are likely bunk anyway so you don't need to not destroy them. It's easy to cut the legs and desolder the remainder if the structural tabs aren't soldered. Clean up the holes with braid. And you'll be done in no time. Then you'll have a properly working instrument you can be proud of and use for the purpose intended. Can see only good things coming from the decision :) Good luck and let us know how it turns out. Cheers, Arkay
-
Hi lifeglug, Would be great if you could fix it electronically but I highly doubt that you'll get a common fix across the batch that could fix it for all encoders equally. In my case desoldering was the only way and what I should have done from the beginning. I spent too long on "what if" and "how come" scenarios. I've since built a second mb6582 and had no problems at all. It's sucks but it's the luck of the draw sometimes. Pick your worst and just desolder that one. That will prove the fix, 14 sounds like a lot of desoldering but like anything if you take your time you can be successful. The feeling of getting it fixed almost makes it worthwhile! Cheers, Arkay.
-
Thanks for looking but in the end I cut a piece of clear plastic to size and glued it on the back of the panel. End effect is pretty much as good as the window anyway. Finished result:
- 1 reply
-
- 2
-
-
Not sure if this will help anyone but I recently made this mod to my mb6582 which worked brilliantly and is in my opinion the best option for powering the machine. I already had the switching vreg from back when altitude created the original post (thanks!). I had a couple of options for getting the 12v supply into the machine: 1. Put a c64 male power plug onto the end of a wall wart. This restricted me to a single (untested) supply that had to have the plug cut off and would create difficulties if I ever sold the machine, particularly over seas. 2. Put a barrel jack into the mb6582. Best option, but seemed too difficult given the mounting options and panel cutout is for the full size c64 jack. In the end I went with a third simple option and created an adaptor to convert any general wall wart into a usable supply. Pics included. I ended up using a wall wart from a Western Digital external drive to power the mb6582. This was an easy solution and cheap to make, and required no additional mods to the mb6582 or panel. The risk of course is someone plugging in a real c64 supply without the adaptor but no one will ever use it but me anyway. If I ever pass it on it'll come with a warning to always use the adaptor with a centre pin +ve 12v 1.5+a supply. Not sure what the effect would be if a c64 supply was plugged in directly but it may even be harmless. The adaptor only requires the +/- female barrel jack to be wired to the correct pins on the c64 male jack. Easy enough to figure out. I can't remember the exact pins off the top of my head but it'll be obvious when completing the mod. Get the plugs as close together as possible and heat shrink the lot and you're done. Cheers, Arkay. Wall wart female plug: To c64 male plug: bit of heat shrink completes the adaptor:
-
Hi All, Hoping someone might have a perspex or glass window for the Wilba style MB6582 lying around unused. I'm finishing up a second machine from long ago and the window really adds a pro look to the build. I have one in my original MB6582 and it looks great so I'd really like to finish this unit the same way. Please let me know if you still have one and we can sort out paypal etc. Thanks. Cheers, Rick.
-
+4 from me, to round out a full set of beer goggles :w00t: :hyper: :geek: :frantics: :D Thanks for all the awesomeness this site provides and the undying efforts of T.K keeping it all running and ticking over with endless improvements. Also a hat tip to Wilba, Hawkeye and the many many frequent and infrequent contributors that make this site so awesome. Merry Christmas to all! :smile: @borfo, great idea for a thread ;) Cheers, Arkay.
-
the first track I have done using Midiboxes some years ago...
Arkay replied to matcom3's topic in Songs & Sounds
Sweet :) Lovin' the Trance. -
I run GNU/Linux and have no problems with a variety of midi equipment. Including a Roland UM-1X. Sounds to me that it's the UM-1G and/or the cheap generic interface that is likely the culprit. Did you checksum the downloaded firmware before flashing? Maybe you had a bad download? Cheers, Arkay.
-
Awesome work T.K! The quantity and quality of your work amazes me :) Cheers, Arkay.
-
Lasercut Acrylic Case+ Frontpanel for SEQv4
Arkay replied to smokestacksproductions's topic in MIDIbox SEQ
MaG2k, Glad you found a workaround with the software. It's an odd one. I can't help with your other questions though. Smokestackproductions conversion just worked for me after a short learning curve in the software to add the extra midi ports and move the SD slot. But I really know little to nothing about designing something like this from scratch in CAD software. This case was my first foray into laser cutting at all. I can see why it becomes addictive though :D Good luck with the case! Cheers, Arkay. -
Lasercut Acrylic Case+ Frontpanel for SEQv4
Arkay replied to smokestacksproductions's topic in MIDIbox SEQ
MaG2k, Not sure what is happening with your inkscape but I can confirm that I used those files in inkscape (on Linux not that it should matter which OS you use), and modified the original to suit before sending off to Ponoko. Everything worked fine when I did it so I'm wondering if there is some setting or oddity in the way inkscape is opening the file? Defaulting to the wrong units of measurement or something? I can't exactly remember now if I used the original files in post 1 or the modified files that flip posted in post #18. Have you tried opening flips in inkscape to see if they exhibit the same issues? If they do then there's something off with the software as it all can work fine with inkscape and either one or both sets of files. I can check on my work laptop next time I'm there to see if I still have the modified files if that will help? Cheers, Arkay. -
+1 for more tutorials. I'd love to see some too. The v4 is so powerful and everyone could benefit from such detailed documentation. Even better would be a user posted tutorial forum where questions on technique could be answered by other members, preferably in video format. Members need to be willing though. If I felt confident enough I'd have a go, but sadly I don't. Would be awesome if an instructional video library from the simple to the complex could be built up! The original videos from TK inspired me to build the v4 and the other videos I've found of the v3 in use have been very inspiring and useful. Just not enough of them :) Cheers, Arkay.
-
That's looks awesome. Nice one :) What center knob do you have on there?
-
T.K. I did find the ability to change the function of the datawheel today while I was messing with the new functionality! Happy to go with your suggestion above and thanks for the effort and the mods :) Cheers, Arkay.
-
T.K. Yep. All fixed. Thanks! One final suggestion. At present after you set the the active step the only way to get to another inactive step is via ff/rew. It seems a little unintuitive that you can't scroll to the final step with the datawheel and then adjust it's value with it's specific encoder. Just wondering if this might make more sense: 1. scroll to the step you wish to be the active step, denoted by > < (all button currently off) 2. turn all on (locking in active step) 3. scroll to the final position via datawheel or ff/rew 4. adjust value with encoder (triggering ramp between active step and inactive step being modified). 5. turn all off to complete. That way you can still scroll around the pattern with the datawheel without changing the selected active step. Would this have any unwanted side effects with the all function itself? Cheers, Arkay.
-
Just tried it out. That's awesome and so quick to edit what I needed to do. Implementation is obvious and works really well. e.g. for those reading the thread if say you want to sweep to a midpoint in a pattern you can set the active step to 64 (midpoint of a 128 step pattern), then set step 0 and 128 to a value of 0 and you've got a perfect 0-128-0 ramp peaking in the middle of the pattern. A 32 beat drumroll is as simple as selecting step 0, velocity 0, hitting "all", then changing step 32 to 100. I think I found a bug though. With the all button depressed if you scroll from position one through to position 17 and greater using the main encoder the display doesn't switch to the next set of 16 steps unless you hit the ff button to force the jump. i.e. if you use the main encoder to scroll through a display boundary the display isn't following the step selection. You can see by the value next to the cc# that the steps are correct but the display remains static only showing the 16 steps you could see when "all" was selected unless ff/rew are used. As a result if you scroll all the way to the end of a 128 note pattern via the encoder, changing the 16'th encoder results in you editing step 16, not step 128. To see step 128 you'd either have to ff to it or turn all off. Loving the functionality already. Thanks for implementing this T.K.! Cheers, Arkay.
-
T.K. Man your are quick :) You sure there's not three of you working on all the things you do!!! I'm out at present but will be trying this out as soon as I get home. Handling sounds fine and I doubt I'll be able to come up with anything more ergonomic but won't know till I try it. Initially I'd thought of a shift like function i.e. Hold select, press a step or tweak encoder to set step start position and initial value, release select, navigate to end position via whatever method user chooses, hold select, press the final step or tweak it's encoder to set the end step and final value, release select. Which seems logical to me. But so does what you've already done ;) Awesome work! Cheers, Arkay.
-
It makes a boatload of sense to my workflow too. I'm forever changing midi channels on the master keyboard (which takes a number of key presses)... Now I can just change tracks on the sequencer :smile: Excellent modification. Cheers, Arkay.
-
T.K., I see what you mean by the dynamic changes and that would be an awesome addition but I also understand why the logic to achieve that is soo much more complex. The static/circlon way would also be of great use. If those pre programmed steps can then be all raised or lowered simultaneously and globally across the track like the circlon then that provides a "live" aspect to it's usefulness. The only other option that I presently see (besides the LFO which works awesome BTW), is to manually edit each step via encoders which is cumbersome. The lfo is great, but is more aimed at continued wavy automation. An editor based solution allows specific ramps to be used, without manually completing each step, but also allows for irregular shaped envelopes. The lfo with a sine wave for instance will give you a nice phase via the amplitude of the wave, but if I wanted to construct a: 0 to 29 step rise over 128 values then a sharp drop down to 50 over the next 30 steps then a further drop to 10 over the next 40 steps it wouldn't be possible via lfo and the only way would be by manually adjusting the values of every step throughout the pattern (100 edits) when in reality 3 "ramp edits" are all that could be required: start 0 end 29 range 0-128 start 30 end 59 range 128-50 start 60 end 100 range 50-10 I absolutely love the idea of the high resolution sweep via higher ppqn but that only matters for the use case when the number of gate steps is less than the range of sweep steps required. I do see the complexity in implementation and possibly even issues with understanding and obviousness of what is going on to the end user from a UI perspective. In reality if a user needs a higher resolution sweep there's nothing stopping them from using a higher resolution for the entire track and then distributing the cc ramps via the same static edit methods. i.e. Setting a start/value and end/value pair and having the editor generate the static steps in between, at what ever resolution the entire track runs at. Obviously large sweeps over small distances would result in low res audible jumps. In that case I probably wouldn't do it. This function is really of use over longer periods. Like increasing the velocity of a snare from 0 to 100 over 32 steps for a long snare roll for instance. Without the ramp function the end user must calculate the size of the increase per step manually and then input that velocity data to 32 steps, one at a time. Possibly a different way would be to change how the sequencer presently works and have a highest ppqn effects track that always runs along side the standard note data in a track when the track contains cc data. i.e. The effects track is always at the maximum resolution and any statically made ramp type edits would automatically yield the smoothest changes between two endpoints. Allow a max of 4 cc numbers per effects track and remove the notion of tracks with gate and cc data combined. So a pattern is either just note date at it's specified ppqn, or note data + a 384ppqn effects track. That might not be practical from a speed perspective, just thinking out loud. I think straight ramp (vector) generation between two points would be a great addition as a time saver, especially if it's easy to implement, that's a win/win :) If it could be made to extend past a single track in song mode, then even better! The higher res methods could be a longer term goal? Cheers, Arkay.
-
TK, Works perfectly for me under Arch Linux. Not what you need to know with regard to Windows but feedback none the less :smile: Cheers, Arkay.
-
TK., Thanks for a very detailed response as always! I'll check out the LFO and eagerly await the additions at a later stage. Love the suggested way of implementing it too. Will make it far more useful than the linear way I'd suggested in that first post. Also great to know that I haven't gone mad and it wasn't sitting in front of me the whole time :D Awesome work you do!! Thanks again. Cheers, Arkay.
-
Hi All, Hoping someone can tell me how or if this is possible with the mbseqv4. I'm wanting to know if I can set a start position and value of a CC# for instance and have the sequencer generate accurate values at each step up to and including an end position and value that I also set. Say I have a 128 beat long pattern over which I'd like to do a filter sweep,. Can I set a cutoff filter at say a start value of 10 on beat 1, and an end value of 100 on beat 128, and have the sequencer fill in beats 2 thru 127 with generated values gradually stepped between my start and end thresholds?. Or I may want a pattern to fade out over 20 beats stating at beat 44. Can I have the sequencer do the hard work for me? This could be used for filter sweeps, easy bass/snare drum rolls using velocity, useful for panning stereo sweeps etc. steps 0-16 gradually increasing from left to center, steps 17-31 gradually from center to right etc etc, copy/paste and repeat for steps 32- 64. Secondly, can this be done across multiple patterns. i.e. If I wanted to arrange filter automation across multiple patterns in song mode can it be done and if so how? Not that I've really progressed to song mode yet anyway but curious minds want to know :smile: Still getting my head around the power and usability of this wicked machine. I'd love to see many many more tutorials and/or videos on it's usage. More so people using it to create (start to finish), rather than the end creations only. A dedicated "how to use" forum would be great for anyone wanting to post tutorials on funky things they've learned to do on the MBSeq too (but I guess that is another thread altogether). What has me thinking like this is the many graphical DAWs that allow a user to simply draw a filter curve or velocity curve (or line), via mouse on screen across a pattern or even multiple patterns. Setting A/B points with interpolation in between would be a fast way of adding such? Then again perhaps I'm thinking about this in all the wrong ways too. Happy to be set straight ;) It'd also be smart if the value changes are less frequent than the number of steps required then the CC#'s are only put in where required rather than at every step. No point sending values of 99,99,99,99,100,100,100,100 etc over 8 steps when you could send 99,nothing,nothing,nothing,100,nothing,nothing,nothing etc... Reducing the amount of midi traffic. Any and all suggestions very much appreciated. Cheers, Arkay.
-
and finally my knobs made it to Aus. Always takes so long... Then the post office lost them for a week!! Ah well. I have them now. Thanks Kristal=!
-
Lasercut Acrylic Case+ Frontpanel for SEQv4
Arkay replied to smokestacksproductions's topic in MIDIbox SEQ
I used a small bottle of model paint from a model aeroplane shop. There is also a thread on how to do infill with wax crayons and a heat gun. That might be something to look into though you'd need to be careful with the heat gun and plastic. The paint worked ok and if I did it again I'm sure I could get a much better job due to the first time experience gained. I think this is what I used: http://www.modelkitsonline.com.au/pages/main/dataAccess.php?Key=2499 It's very difficult to paint into the cut-outs, better to dab over and fill the crevices, wiping excess around the cut-out away with a cloth, wait for them to dry a little, then repeat, each time buiilding up another layer of paint in the infill. The more you do and the more patient you are during this step the better it will turn out, aim to fill the lines so they are mostly full but still have a dip and are not completely flat (or sitting above the level of paper). I also removed the paper very slowly and carefully from mine not long after the final paint run was done as I wanted the paint partially wet so there was no chance the paper would pull dried paint out of the infill. I then used a fine blade to clean away any excess paint and the inside of cut-out letters (like the triangle at the top of an A or the inside of a D for example). It comes out pretty good done this way. Just take your time. Any mistakes can be cleaned away with mineral turps without damage to the plastic though white paint on a black matt surface will not completely clear away and a light hazy residue can sometimes remain. Good luck with it. Be sure to post up some photo's of the finished product :) Mine has been working great and my parts for my other 4 midi outs are now on their way too. Wish I'd have build them in to start with as I don't really want to disassemble it but I need to ports so don't have a choice. Cheers, Arkay. -
schweet :D