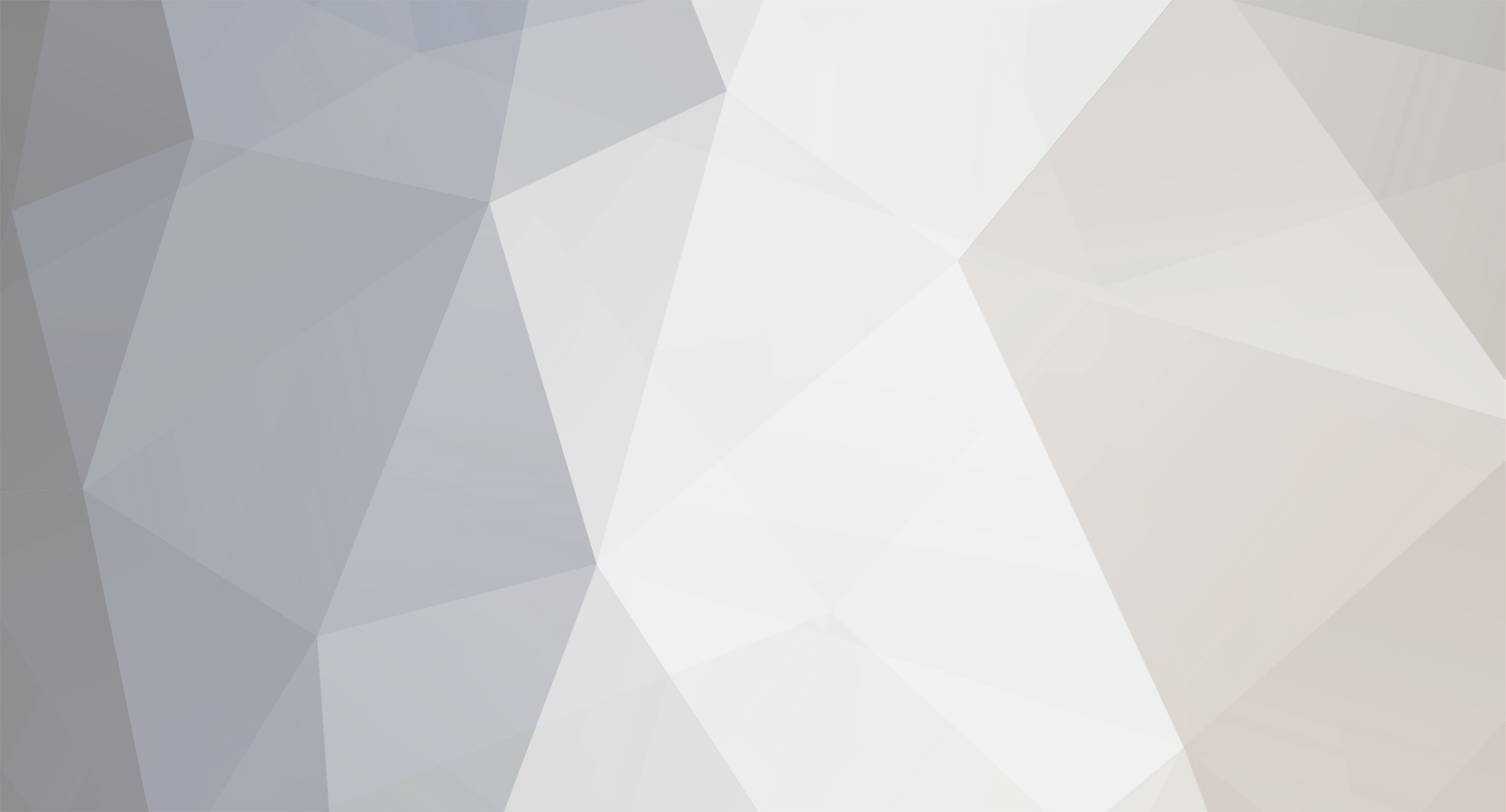
Zam
Members-
Posts
625 -
Joined
-
Last visited
-
Days Won
26
Content Type
Profiles
Forums
Blogs
Gallery
Everything posted by Zam
-
plz wait until OP say something...can be dumb too Still (no offense) I find pples around so focused on digital and code that they usually miss the first things to check in the chain Best Zam
-
Hello Did you check the analog side ? I mean the pots to multiplexer path ? If you make the 8 pot wiper like a single bus... Best Zam
-
KiCAD is great ! Glad you switch Best Zam
-
Hello Why not just use a resistor/fuse (or resetable fuse) and a zener ? Best Zam
- 5 replies
-
- sid 8580
- power supply
-
(and 1 more)
Tagged with:
-
Hello Thorsten I have something like "MF_HD" in head since time but don't start because of no more real need for me (I have my motor driver) It's hybrid, between MF_NG and My 89MotioN, in all aspect probably (cost, quality and performance) Your two AD scan from fader servo seem to show improved noise at 200kHz. Best Zam
-
Ok ! don't know what is the agenda or if any major MFNG update is on the road (which I can help on by the way...) I suggest to factor at least 10 the clock in case of hybrid system (analog close to or in the fader...) let say 312.5kHz , which correspond to 256 speed level (you have room over 64...) also a value over 192kHz (HD audio) I mean If it's easy don't hesitate to change this... Best Zam
-
Hello Thorsten That's interesting, what is the max possible clock speed ? Best Zam
-
Hi all Look promising Especially if RTPM via wifi is implemented Best Zam
-
Hello Fader are just pot, 3 pin, you should find the pinout within 30 sec with a ohm meter... The pin that have variable resistance (across any two other) when moving the fader is the wiper The two pin that have fixed resistance when moving the fader are 0 and Vref The pin across the wiper which indicate low resistance when moving the fader down is the 0v The pin across the wiper which indicate low resistance when moving the fader up is the Vref Best Zam
-
Hey TK of course...my bad Best Zam
-
Hello If you need more toggle steps use a map for value MAP 1 2 3 4 in event button range=map1 the button value will toggle 1,2,3,4,1,2,3...... and 4 sender with contitional if_equal=1.... if_equal=4 i think i made a mistake you have to separate the fwd_id led (otherwise led will get the sysex and not the button value) event_button id=1 fwd_id=sender:1 range=0:127 button_mode=toggle event_sender hw_id=1 id=1000 type=SysEx stream="0xf0 0x00 0x01 0x16 0xE0 0x18 0x10 0xf7" if_equal=0 event_sender hw_id=1 id=1001 type=SysEx stream="0xf0 0x00 0x01 0x16 0xE0 0x18 0x01 0xf7" if_equal=127 event_sender hw_id=1 id=1002 fwd_id=led:1:0 if_equal=0 event_sender hw_id=1 id=1003 fwd_id=led:1:1 if_equal=127 Best Zam
-
Hello You can do it this way: event_button id=1 fwd_id=sender:1 range=0:127 button_mode=toggle event_sender hw_id=1 id=1000 fwd_id=led:1 type=SysEx stream="0xf0 0x00 0x01 0x16 0xE0 0x18 0x10 0xf7" if_equal=0 event_sender hw_id=1 id=1001 fwd_id=led:1 type=SysEx stream="0xf0 0x00 0x01 0x16 0xE0 0x18 0x01 0xf7" if_equal=127 Best Zam
-
Hello Don't know if it's related but I remember having app issue (MB_NG) when in debug mode combined with large "regular" data transfer or config file update from/to computer. So maybe as a start just be sure debug mod is off as soon as you don't need it and send lot of data. Best Zam
-
Hello If you reset (button) the core wile pressing (and keep pressing) user (button), you should start the core in bootloader mode. MIOSstudio should recognize and connect via USB, as hex upload working to update/load your mios app. Just keep your finger at user button all the time, if you release it the core reboot. Best Zam
-
Hello Welcome here ! What hardware did you build ? did you install the bootloader ? We need more information to help you. Best Zam
-
Hello Can't say... you have to try in your design Here I run aprox 35cm wire and trace from 10 to 25cm, with 3 connector in the path, from pot to AINSER input pin Vref have dedicated regulation. No jitter at 11bit Side note, I use AINSER8, no multiplexing, can't say what is the noise introduced by switching nor if there is some. IIRC you can chain AOUT up to 4 TLV (32 out) with a single RC line, so yes, 64in/16out is possible at J19 Best Zam
-
Hello You don't need a second one ! assuming you talk about midi resolution ? Set your AINSER module at 11bit in NG, and set event type= according to your requested resolution (7 or 14bit) NG should scale With proper design and dedicated ref regulator you should go up to 11bit Best Zam
-
The HAARP, a Hardware Advanced Arpeggiator.
Zam replied to Antichambre's topic in MIDIbox User Projects
that's definitely even better Best Zam -
The HAARP, a Hardware Advanced Arpeggiator.
Zam replied to Antichambre's topic in MIDIbox User Projects
@Antichambre Look great !!! so J18 for MCAN ? Best Zam -
Hello maybe this ? kb_transpose=<-128..127> Only valid for EVENT_KB: specifies the transpose value for the played key from -128..127 Best Zam
-
By using highend dual track motor fader with one servo track (linear taper) and one audio log track Best Zam
-
I'm sure that audio pass through my fader Best Zam
-
sorry, I mean 15/100 millimeter, If you draw a (quarter) circle of 1mm diameter inside a 90° angle That's what I say, add 3/10 mm and you'll be fine for a soft mount, dust won't come in that much and aestheticly it's not noticeable Best Zam
- 16 replies
-
- midibox fm
- mbfm
-
(and 2 more)
Tagged with:
-
yep... almost two years back (thinking about one) but more precisely, this is not the app (.hex) but the change in code. You can copy/replace that at the correct place, IIRC the only change I made to "fake" raw dual CC as NRPN (note that standard NRPN won't work any more but HUI don't use it) I can also provide the compiled app which should be based on NG1.035 or 1.036 (don't remember what's up at that time), so not up to date regarding newer implementations. Best Zam ps: I sent you an email earlier today